一、背景介绍
某变速器是法士特公司众多变速器中的重要产品,对占领国内以及国际变速器市场有着重要意义,从某变速器诞生至今,产品也在不断的优化。近期某变速器在疲劳寿命试验中发现,变速器一轴有掉落铁锈粉现象,将变速器从试验台架拆下后,发现一轴磨损、锈蚀严重,且台架一轴适配器也有磨损现象。为了避免影响疲劳试验结果,同时减少台架一轴适配器的损坏,对此变速器一轴磨损锈蚀原因的分析,以及对这种磨损现象的改进是很有必要的。
原理分析:在此变速器进行疲劳寿命试验中,若一轴轴头无支撑,在试验过程中,因一轴轴头摆动量大,会导致一轴外花键与台架适配器内花键的磨损加剧,这样不仅会降低适配器的使用寿命,而且也有可能导致因花键磨损而引起的振动加剧,进而导致一轴支撑轴承的损坏。若在一轴轴头增加一个支撑,将一轴轴头固定住,与一轴轴承形成双支撑,则可以降低一轴的摆动量,减少一轴花键与台架适配器的磨损。
二、一轴轴头支撑设计
为了改善某变速器的一轴磨损锈蚀现象,可以在变速器一轴轴头处设计尼龙块支撑,尼龙块支撑(一轴轴头支撑)结构图如图1中2所示。
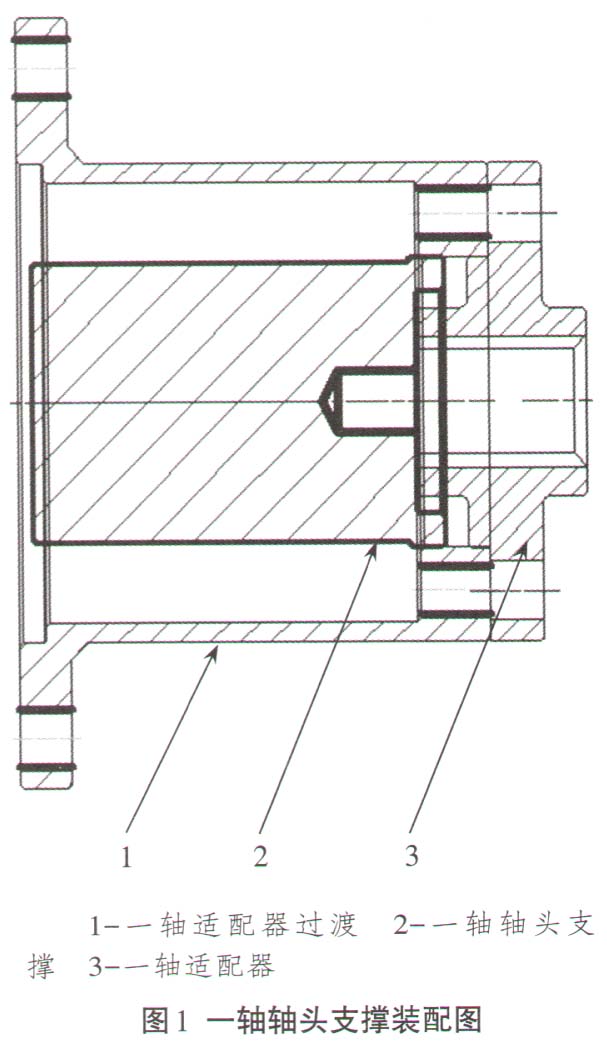
在实验中心试验台架上,一轴轴头支撑与一轴适配器过渡、一轴适配器的装配图,见图1所示。装配过程为:一轴轴头支撑2与一轴适配器过渡1相连,一轴适配器过渡1与电机轴相连,一轴适配器3与一轴适配器过渡1相连。变速器一轴从一轴适配器3右端插入,一轴轴头在支撑2中孔的部位得到有效支撑。
改进之前变速器一轴轴头部位没有支撑,一轴轴头相当于一个悬臂梁,试验过程中摆动量较大,增加支撑改进后,一轴轴头的摆动得到了有效控制。
为了验证增加支撑的可行性及正确性,以下分别从理论仿真分析和台架试验二方面着手进行验证。
三、仿真分析
针对某变速器一轴轴头无支撑和添加支撑2种状态进行仿真计算,对比一轴轴头在受载下的变形量。这里选取汽车行业广泛使用的Romax软件来对变速器建模,各零部件建模均细化,加载方式和位置均与变速器实际工况一致。
变速器一轴输入扭矩取此变速器的额定扭矩,取某一挡位进行分析(这里取1挡,因1挡时,变速器输入和输出扭矩差最大,对一轴轴承处所受扭矩和转速也最大,由此对一轴影响最大)。图2与图3分别是一轴轴头无支撑位移图和一轴轴头有支撑位移图。
由有限元计算结果(图2和图3)可以看出,一轴轴头在无支撑状态下,轴头的最大位移量约为800μm ,一轴花键处最大位移量约为600μm ;一轴轴头在有支撑状态下,轴头的最大位移量约为22μm,一轴花键处最大位移量约为24μm。
由以上位移数据可以看出,一轴轴头在无支撑状态下,最大位移量比有支撑状态下一轴轴头最大位移量大30倍左右,由此得出,一轴轴头在有支撑的情况下,可以大大降低一轴花键与台架适配器的磨损。
四、试验验证
在设计并且制作好一轴轴头支撑后,在实验中心某变速器性能及疲劳寿命试验台上进行此变速器的疲劳寿命试验,分别进行了一轴轴头无支撑和添加支撑2种状态进行对比,共进行了多次试验,在每次试验完成后,拆解变速器观察一轴磨损锈蚀程度,这里取1组照片进行对比,见图4所示。
由图4中图片对比可以看出,一轴轴头在有支撑的情况下,一轴磨损锈蚀程度降低,并且也减少了台架一轴适配器的损坏,同时也避免了因磨损导致的试验过程中异常情况发生,因此,在试验中应推广。
五、总结
本文通过在某变速器一轴轴头处添加支撑,改善了此变速器在疲劳寿命试验中一轴磨损锈蚀现象。该支撑安装简便,成本较低,不仅改善了变速器一轴磨损锈蚀的现象,并且避免了台架一轴适配器的损坏。此方法可为类似变速器试验提供指导借鉴作用,提高了试验的成功率,避免了变速器非正常工作状态下产生的影响。