在车身覆盖件修复和质检过程中,一般使用样规(行业内也称卡规、样板或卡板)来检查面板弧度及平整度的恢复程度。样规检测的原理是在损伤前面板或对称侧面板的固定位置上事先制作好弧度吻合的样规,而损伤后的面板由于曲率发生了变化,当再次把样规放在该位置时必然会产生不贴合的现象,维修或质检人员可以通过观察、测量样规与修复后面板当中形成的缝隙的宽窄、长短来评判面板的修复情况。
常用的样规有三种,分别是成型样规(图1)、针式样规(图2)和自制样规(图3)。成型样规一般专车专用,多用于比赛时的评分,造价也相对较高。相对于成型样规,自制样规的使用位置灵活,几乎可以用于车身表面任何需要的位置。针式样规虽然位置灵活,但总体精度不及成型样规和自制样规。其次,自制样规的制作成本较低,由于具备了上述优点,为了保证面板的修复效果,自制样规使用得最为广泛。
自制样规利用金属冷制工艺中的放边原理,按照一定的规律对3mm厚的纯铝条进行敲击和锉削加工,使其侧面成为符合车身覆盖件弧度的模板,理想情况下,该模板应该可以和车身面板完美贴合,接触面(测量面)没有任何间隙。在实际操作中,往往利用车身同一部位对称侧没有受损部位的形状和弧度作为制作的依据,在受损面修复后用样规来检测修复质量。在各类比赛当中,则一般是在制作面板损伤前就做好该部位的样规,待到面板修复后对修复质量进行检测。然而,困扰自制样规使用的最大问题是该方法极大地受限于制作人的技术水平。为使接下来的涂装步骤顺利进行,常见的修复标准是修复后面板不能高于原表面,低于原表面的容差不能超过1mm。也就是说,这对自制样规的精度提出了极高的要求,如果样规本身与原表面的贴合度超过了1mm的容差,那么用该样规检测修复质量就没有实际意义了。同时,为了检测一处损伤一般至少要制作横三竖三共六把样规,还要考虑到时间成本。因此,在有限时间内进行高精度样规的制作是制约这一检测方法使用的最大障碍。对于熟练的钣金工,20min内就能使用铝条制作出6条容差0.5mm左右的精度较高的样规(数据来源于世赛中国集训队训练统计),可是如果需要进一步提高精度,那么时间成本是非常高的。对于不够熟练的操作者,可能费了一番周折也只能制作出容差在2mm左右的样规,然而即便是新手,也能够迅速制作出2mm精度的样规。基于以上的岗位工作需求,经过反复的实验和摸索,笔者探索到一种使用低温热熔塑料快速制作高精度面板样规的方法。
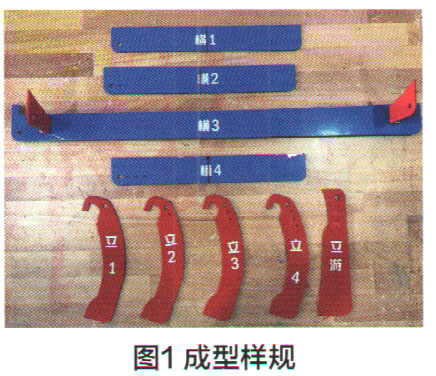
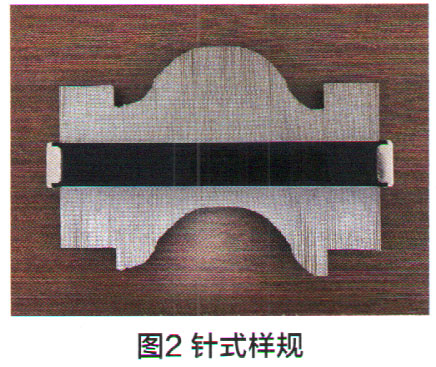
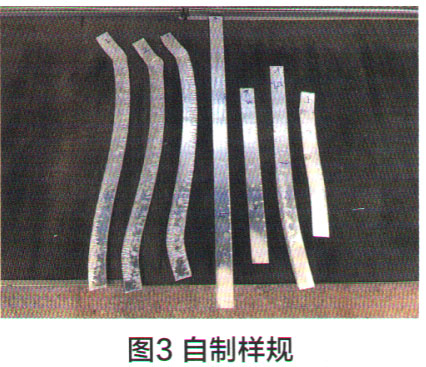
低温热熔塑料,学名聚已内酩,英文名Polycaprolactone,简称PCL,是一种无毒、可生物降解的有机高分子聚合物,广泛地应用在手术缝合线、医用造型等领域。随着生产成本的降低,近年来作为一种新型制模材料,应用拓展到艺术造型和儿童玩具等行业。商品化的低温热熔塑料外观为白色塑料颗粒(图4),其在70℃以上的热水中,可以转化成透明无色的半固态物质并且具备了可塑性(图5),可对其进行塑形加工,当材料恢复到室温或人工进行降温后,再次转变为白色,此时之前的塑形会得以保留并失去可塑性,硬度恢复到塑形前的状态。这个变化过程是可逆的,在重复加热、冷却中可反复出现多次,随着次数的增加和杂质的不断混入,材料的结合能力慢慢变差。根据使用条件的不同,在进行5-10次的反复塑形后材料失去使用价值。值得一提的是不同品牌的低温热熔塑料具有不同的收缩率,应尽可能选用收缩率小的低温热熔塑料颗粒,制作时尽量不要使材料产生过厚的堆积,以免降低自制样规的精度。
在第44届世界技能大赛全国集训队5晋2选拔赛中,使用低温热熔塑料制作高精度样规的方法得到了极佳的应用。由于晋级赛分为三轮,分别要在上海、云南、郑州3个集训基地的赛场进行,比赛用车身经过长途跋涉抵达赛场时面板难以避免地产生了变形,无法使用一套公用的成型样规对所有五台车身进行检测。为保证比赛的公平性必须根据每台车身面板变形的不同情况制作相应的样规,这就要求必须在极为有限的比赛准备时间内制作出5套高精度的样规。下面以,套6把样规为例介绍制作过程。
[1] [2] [3] 下一页
关键词: