3 电刷镀工艺
3.1镀前准备
(1)表面预处理。镀件表面应尽量光滑平整,应去除零件表面的毛刺、飞边,以免划破阳极包套。如零件有缺陷,例如划痕、擦伤或锐边的凹坑等,为了防止应力集中和保证修复质量,应将其根部和表面凿宽。凿宽的宽度应大于原来深度的2倍。根部和表面边缘都应圆滑过渡。如表面有密集的小坑或划痕,应将其去除。轴或孔如已磨损,应进行加工以消除其圆度及圆柱度误差。键槽和油孔可用石墨堵塞填平,以免边缘因电流集中而引起脱落。不需要修复的相邻部位需用绝缘漆或胶带纸加以保护。
(2)机械或化学方法去锈及除油。零件电刷镀前必须去锈、除油。一般用钢丝刷、喷砂或砂纸去
除锈斑;用汽油、丙酮或四氯化碳去除油污。
(3)电净。电净是利用电净液通电后组织成分离解,在零件表面形成气泡,机械地把油膜撕裂,而电净液中的乳化剂则产生强烈的乳化作用,把油脂清除掉。其反应式如下:
阴极4H2O +4e =2H2 +4OH-
阳极4OH--4e=O2 +2H2O
可见,在阴极上生成的气泡多于阳极,除油效果较好。所以在电净时零件一般接负极。但是对一于高强度钢,为了防止渗氢,电净时零件应接正极。电净后用清水彻底冲洗零件表面。
(4)活化。活化是利用专门的活化液,通过电化学作用,彻底去除零件表面的氧化膜和其它杂质,从而露出新鲜基体金属,使镀层能与基体金属牢固地结合。活化时,零件的极性视金属材料和活化液的种类而定。
3.2电刷镀
为了得到结合强度高的镀层,并满足零件表面的各种工况要求,需要有针对性地合理选择镀液及其镀层的组合。一般包括起镀镀层(底层)、尺寸镀层(包括夹心镀层)和表面工作镀层3种。
(1)起镀镀层。俗称底层。各类镀层在不同的金属材料上的结合强度是不一样的。有些电镀液,如高速铜-II,它不能直接沉积在钢铁上,因为两者之间电位差太大,强烈的置换反应会造成基体金属的严重腐蚀。有些镀层,虽然和某些金属的结合很好,但长期工作后会产生电化学腐蚀,或者因为互相扩散而降低其效能等。因此要镀一层底层,在工艺上称起镀镀层。实践证明,特殊镍和碱铜是较理想的底层,适用于各种钢、铸铁、镍、铜、铬、铝及其合金等。电刷镀时零件接负极,厚度为0.002~0. 01μm。电刷镀特殊镍时,先作无电擦拭2~5s后再接通电源,可改善镀层与基体的结合强度。
(2)尺寸镀层。是指专门恢复零件尺寸的镀层。对于单一的金属镀层,随厚度的增加,其内应力逐渐增大,晶粒变得粗大,裂纹增多,其结合强度和镀层本身的抗拉强度也随之下降。在镀层过厚时,甚至会引起镀层的脱落,所以单一金属的镀层厚度应适当加以控制。单一金属镀层的安全厚度可参阅表1所示。
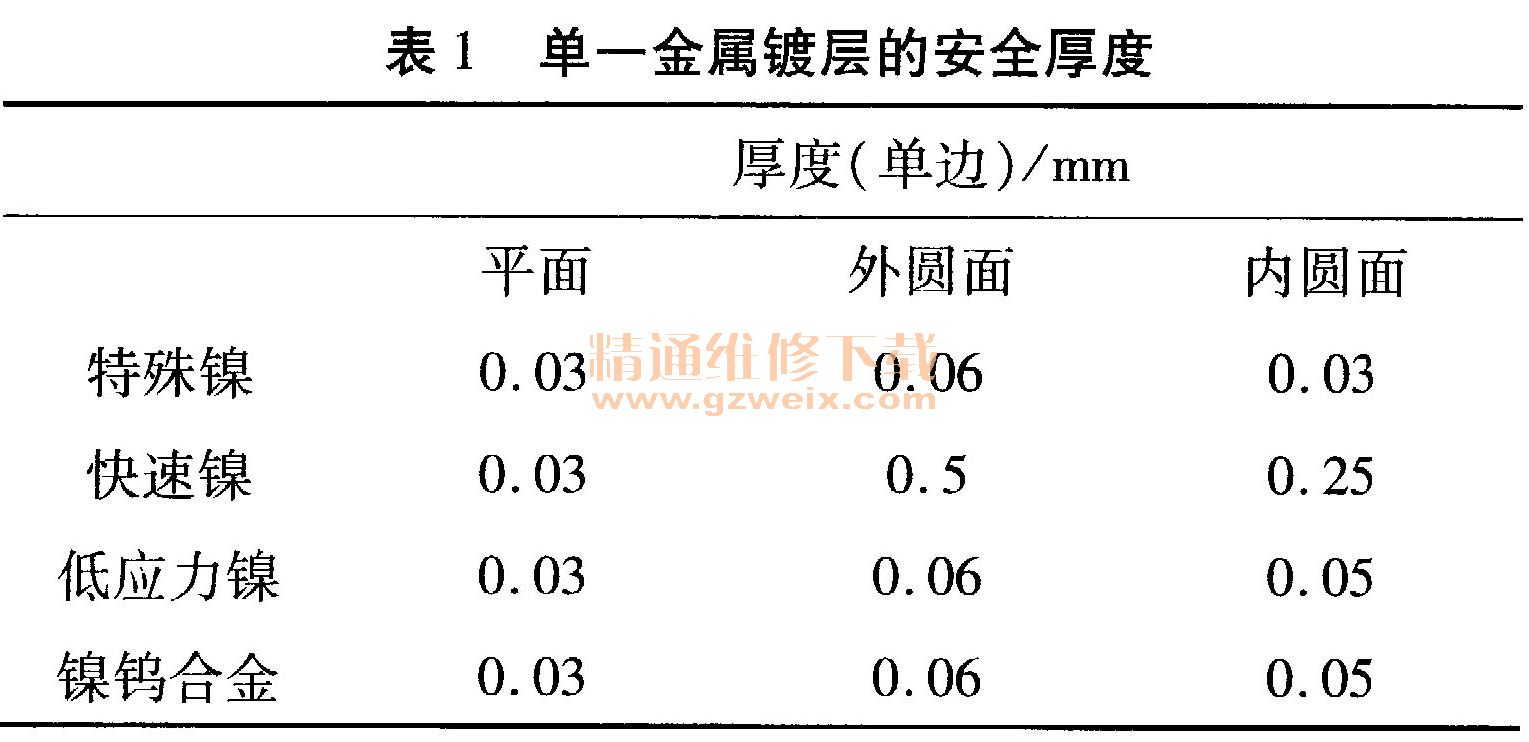
(3)工作镀层。工作镀层是零件表面的最终镀层,其作用是满足零件表面的机械物理性能等特殊要求,比如耐磨镀层或装饰性防蚀镀层等。镀层结构的选择应根据被镀零件的具体情况而定。镀完后一般不需要再进行加工,必须加工时,可采用绿色碳化硅砂轮磨削加工。
4 影响电刷镀质量的因素
(1)工作电压和电流。电压低时电流较小,这时金属沉积速度慢,镀层光精细密,内应力小;电压高时电流相对较大,沉积速度快,镀层粗糙、发黑,甚至烧伤。工作电压与电流的选择应与镀液温度、阴阳极相对速度相匹配。
(2)阴阳极相对速度。阴阳极相对速度太低时,镀层粗糙,脆化,有时造成镀层发黑,烧伤;阴阳极相对速度太快时,电流效率和沉积速度降低,甚至不能沉积金属。刷镀时应考虑与电参数相匹配,电压高、电流大时,相对速度也应大些。
(3)镀液与工作温度。工作与镀液的温度均在50℃左右时,沉积速度快,内应力小,晶粒细密,结合强度高;温度较低时,应降低电压起镀,待工件温度升高再提高电压;温度过高(>70℃)时,则镀液蒸发加快,沉积速度降低。
(4)被镀表面的湿润状况。被镀表面应在电刷镀过程中始终处于湿润状况,否则会使镀层钝化,继续刷镀会影响刷镀层的质量。
(5)镀液的清洁度。刷镀溶液必须保证纯净、清洁,严防污染,特别要防止各种镀液的交叉污染。
(6)刷镀前应多准备几个包裹好的阳极块,在进行电净活化、刷镀过镀层、刷镀工作层等工序时分别使用,每一包裹好的阳极块只能使用一种电镀溶液,不得通用、混用。
上一页 [1] [2] [3] 下一页