EPB(Electrical Park Brake)即电子驻车系统,采用电子按钮取代了传统的拉杆手刹,通过 EPB 开关或换挡操作完成车辆的自动驻车/释放功能。
一、 电子驻车系统主要组成部分
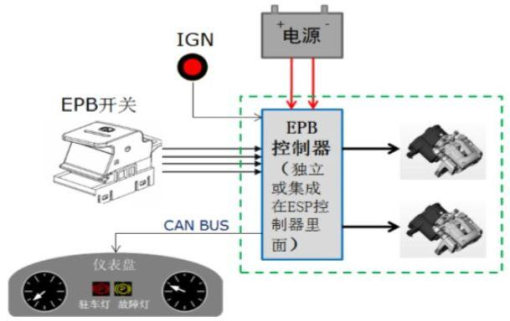
EPB 电机驱动总成在
EPB 电子驻车系统中作为驱动执行机构与制动钳体分总成通过紧固螺栓连接。在
EPB 开关进行拉起/释放操作时通过正转/反转对钳体内部螺杆组件进行力矩传递,进而实现摩擦块的夹紧/释放。
集成式电子驻车后卡钳电机驱动总成有四种状态:泛博电机、海翔铭电机(6 齿和 12齿)、科达利电机。
1、泛博电机(输出轴 6 齿、端口 4 针脚)
2、 海翔铭电机(输出轴 6 齿、端口 2 针脚)
3、 海翔铭电机(输出轴 12 齿、端口 2 针脚)
4、 科达利电机(输出轴 12 齿、端口 2 针脚)
故障现象:仪表提示“请检查电子驻车系统”,
EPB 模块显示故障码为“执行器故障”或
“卡钳电机线路故障(开路)”。检修方法如下:
1、通过诊断仪读取
EPB 模块故障码信息(至少保留控制器软件版本、故障码信息、
数据流信息、 ESP 故障码信息的相关照片记录)。
2、清除故障码,车辆熄火断电静置 5 分钟,等仪表
EPB 状态灯熄灭后,重新上电, 通过
EPB 开关进行 3 次正常拉起/释放,确认故障是否重现(如发现有 ESP 等其它模块相关历史故障时,同步清除)。
3、若故障消失,则为偶发故障。需排查周围干扰因素(如整车启动电压、整车
蓄电池电压波动-特别注意夏天空调高频使用时期、
蓄电池的电量使用情况、通讯信号、 CAN 信号等)。
4、若故障再现,用诊断仪读取
EPB 模块故障码, 如显示为当前故障,车辆熄火断电静置。
5、分钟,等仪表
EPB 状态灯熄灭后,拔掉
EPB 电机驱动线束接插头,检测电机驱动总成端口针脚之间是否导通,电机内阻是否有阻值(4 针脚的泛博电机测 1 号和 4 号针脚,阻值大小仅做为通断参考,不作为电机合格与否的判断依据)。
若导通、有阻值,表示电机驱动总成功能正常,需排查周围干扰因素。如
蓄电池启动电压、 线束与电机驱动总成公端和母端接触不良、检查线束跳动段是否存在内部导线断裂/虚接情况、 电机线束 3 段接插头密封/接触情况、 线束压舌松动、回退、间隙大等。 (排查方法为:检测线束正负两端通断,折叠跳动段线束,观察线束两端是否存在断路/阻值大幅波动)。若不导通或阻值为 0,重新接插电机驱动总成线束, 车辆启动后通过
EPB 开关执行拉起/释放或换挡操作, 电机驱动总成仍无法正常工作, 可初步判断为电机驱动总成故障, 经交叉验证确认故障存在,更换电机驱动总成(至少保留电机驱动总成端子、电机驱动总成端子间电阻检测的相关照片记录)。
注: 插拔
EPB 线束、 电机驱动总成连接线束,车辆必须熄火断电静置 5 分钟,等仪表
EPB状态灯熄灭后进行, 以确保
EPB 控制器进入休眠状态。车辆熄火断电后,电子驻车控制器不会立即停止工作,会有 12 秒至 5 分钟的静态巡检, 这段时间如果对电机线束或
EPB 线束进行插拔操作, 会出现断路现象,导致电子驻车控制器报警,产生当前故障。
5、如以上排查仍无法确定异常点,将电机驱动总成进行 A-B-A 交叉验证后故障未出现,可确认非电机驱动总成故障,需排查其它疑点;交叉验证后故障现象随故障件转移,确认为电机故障,进行更换(需保留交叉验证后电机驱动总成在测试车辆上表现出来的当前故障码相关照片记录)。
6、更换新电机后车辆需重现上电启动,进行至少 1 次正常的拉起/释放,并清除
EPB 控制器模块内部历史故障码。
注:更换电机驱动总成,车辆必须熄火断电静置 5 分钟,等仪表
EPB 状态灯熄灭后进行,
历史故障: 指之前点火周期内发生的故障,现在已恢复正常,可以正常使用。
当前故障: 指当前点火周期内还在发生的故障, 现在故障现象依然存在, 仪表报警无法消除。
三、 更换电机驱动总成注意事项:
1、电机驱动总成可以单独更换,拆解时使用工具不可以磕碰电机驱动总成端盖焊接面,如下图非接触区域。
2、拆解电机驱动总成需在电子驻车处于完全/维修释放状态进行,更换新电机时需保持卡钳安装面和电机配合面清洁。电机驱动总成沿钳体轴向方向平推装入,确保 O 型密封圈无缺失、损坏、挤压变形或破损。
注: 电机驱动总成装配过程中如发现齿槽对接困难,可使用内六花扳手对螺杆内花键孔做轻微调整(调整角度不超过 15°, 避免内部结构损坏),禁止暴力拆装或不执行预装, 禁止通过紧固螺栓直接将电机驱动总成装在钳体上。
3、用专用工具通过紧固螺栓将电机驱动总成装配至卡钳,装配使用售后包中的新螺栓。螺栓装配力矩 8±2N.m。 装配后检查,确保密封位无间隙、密封圈无挤压变形;线束接插牢靠,有线束卡扣时,注意不要漏装。 电机驱动总成换件操作完成后,需进行完全/维修拉起操作, 并用诊断仪清除历史故障码,以避免由于维修操作产生的历史故障现象, 对产品后续正常使用/监控产生干扰。