3 分析验证案例
某款多功能越野车在道路强化路试阶段,试验工程师反馈车辆在经过正弦路、搓板路和比利时路时,B柱下部区域、顶盖前横梁与侧围搭接区域有异响。
3.1顶盖前横梁与侧围搭接区域异响
将顶棚拆解后,对异响车辆进行路试,在通过正弦路时,车身扭曲,可以明显听到哒哒哒的异响声音,确定为钣金件之间的摩擦音。对异响位置进行确认,发现搭接区域焊点布置不合理,且焊点距离钣金边界较远,钣金搭接边宽度较大(55 mm)。车辆经过正弦路,车身钣金扭曲变形,使钣金件之间摩擦和干涉,造成异响发生。调整钣金搭接缝隙后,路试异响消除。为了防止钣金再变形回来,临时在钣金缝隙之间增加快干胶处理。之后的永久措施为,重新设计钣金型面,只保留焊点位置搭接,其余位置增加凸台,避免大面积搭接(图1)。
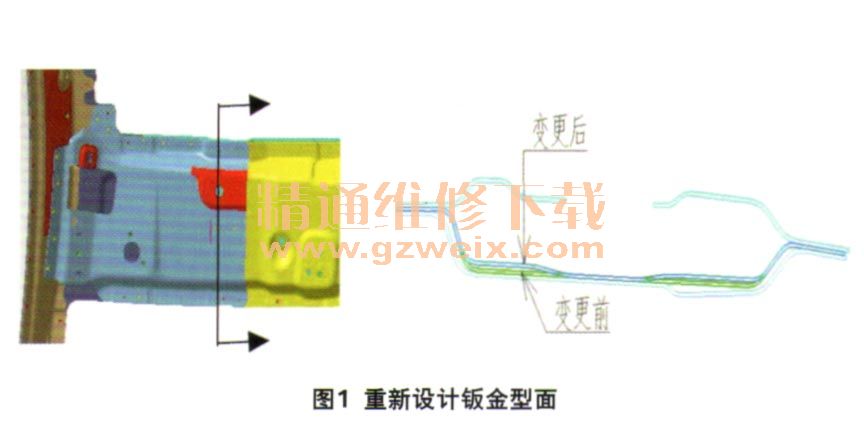
3.2 B柱下部区域异响
对异响车辆路试,确认异响位置处于B柱与地板门槛梁搭接区域。用一字改锥插入到钣金缝隙内,异响消除。对数据进行排查发现,此处由于受车身结构及焊接工艺的限制,B柱内板与B柱加强板在此区域贴合面积大,且无焊点。地板门槛梁与B柱内板只能布置3个点焊,其余位置布置6段CO2保护焊,CO2保护焊只能约束2个钣金件的边缘,在车身变形、振动时,2个钣金件形成变形和振动,造成异响。通过将贴合面减小,同时在B柱内板与B柱加强板搭接位置增加点焊结构胶,在地板门槛梁开2个塞焊孔,使地板门槛梁、B柱内板和B柱加强板3个钣金件形成焊接,在地板门槛梁和B柱加强板区域(图2)增加点焊结构胶,填充钣金件之间的缝隙,避免钣金变形造成的异响。以上方案实施后,车辆无异响问题发生。
4 车身设计再发防止措施
根据车身异响的发生机理及整改措施,制定车身设计阶段的再发防止对策。具体需要注意:钣金边界直接的距离(图3);特征避让圆角设计规范(图4);焊点间距布置要求(图5);CO2保护焊设计。
原则上不允许设计CO2焊接,必须设计CO2焊接时,每个CO2设计一个贴合面,贴合面宽度L≤20 mm。如设计为塞焊,塞焊点距离贴合面边沿L≤15 mm。涉及到3层焊接时,采用塞焊工艺进行,保证3层板都能贴合。
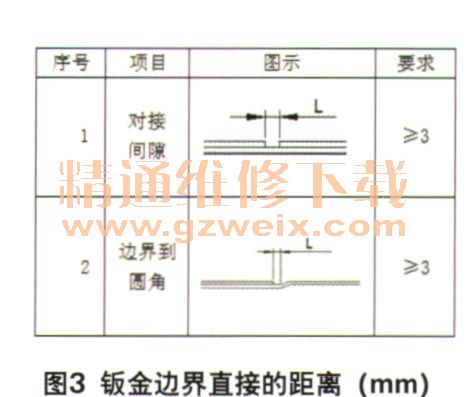
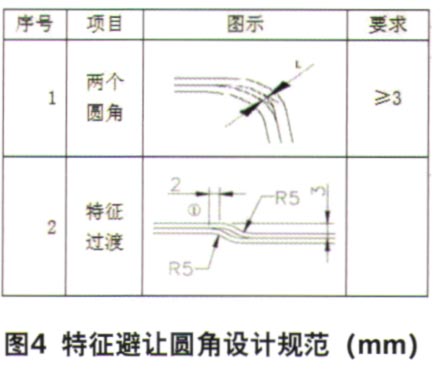
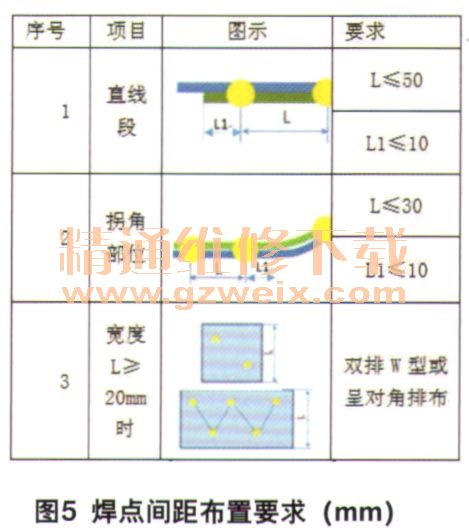
5 结束语
由于车身钣金异响涉及到的影响因素较多,排查和解决问题存在很大困难。目前行业内还没有企业能完全杜绝车身钣金异响,只能采用具体问题具体分析的原则,在实践中不断总结经验,完善设计标准。本文总结解决车身异响的常见方法和再发防止要求,为新项目提供设计依据,共同提高整车感知质量。
上一页 [1] [2]