五、编程器刷片方法
编程器主要用来修改只读存储器中的程序,编程器通常与计算机连接,再配合编程软件使用,如图23所示。在维修时通常使用编程器刷新主板BIOS芯片、显卡BIOS芯片、网卡启动芯片、EEPROM串行芯片等。
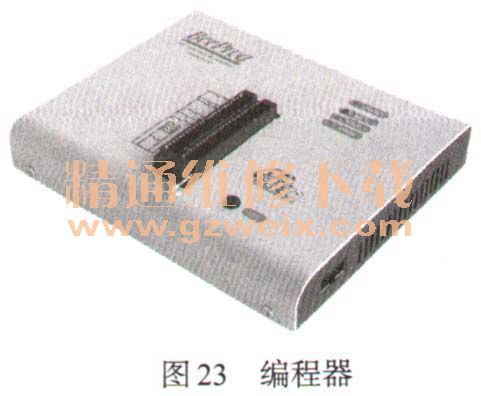
编程器的使用方法如下:
1)将被烧写的芯片(如BIOS)按照正确的方向插入烧写卡座(芯片缺口对准卡座的扳手)。
2)将配套的电缆分别插入计算机的串口与编程器的通信口。
3)打开编程器的电源(电源为12V),此时中间的电源发光管指示灯亮,表示电源正常。
4)运行编程器的软件,这时程序会自动监测通信端口和芯片的类型,接着从编程软件中调入提前准备好的被烧写文件(.hex文件)。
5)编程器开始烧写程序到芯片中。烧写完成后编程器会提示烧写完成,这时关闭编程器的电源,取下芯片即可。
六、电烙铁及其使用方法
电烙铁是维修当中必不可少的焊接工具,它可以将焊丝熔化,将元器件的引脚和电路板的插孔焊接在一起。
6.1电烙铁
常用的电烙铁有两种,即内热式和外热式,如图24和图25所示。
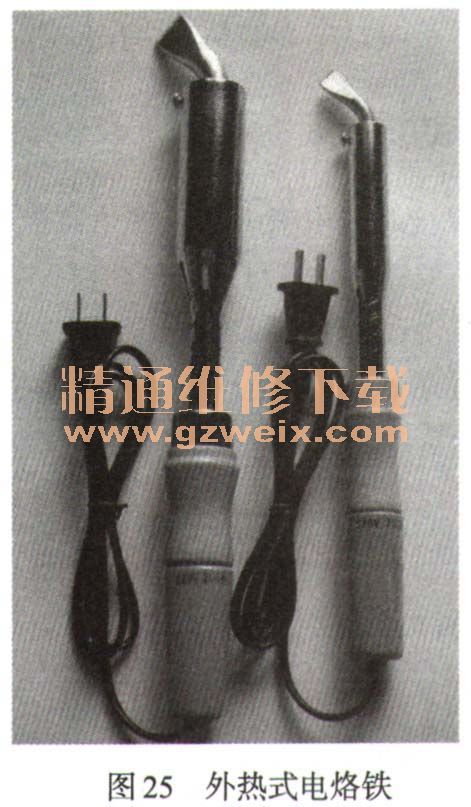
内热式电烙铁因其体积小、价格便宜、发热效率高、更换烙铁头方便等特点,成为一般用户的最佳选择,功率一般为20~30W。外热式电烙铁的特点是功率高,一般为45~75W,可以焊接金属底板或一些比较大的元件,通常在专业加工和批量焊接时使用。
6.2焊锡
焊锡是焊接的材料,有锡条、锡块、锡球、锡丝等,其中最常用的是锡丝,如图26和图27所示。
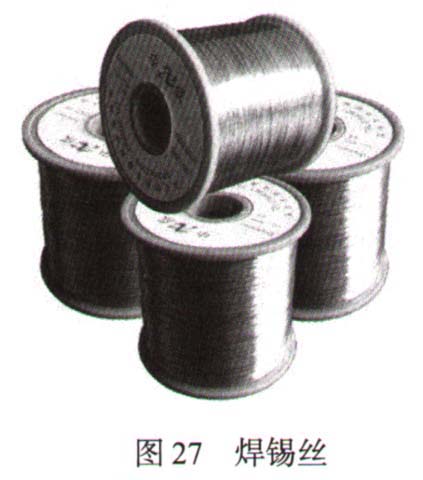
焊锡一般由锡和铅混合而成,锡和铅的比例大概是2:1,在400℃左右就会熔化。通常我们使用的焊丝叫作药芯焊丝,在焊丝中间有助焊药剂,如图28所示。
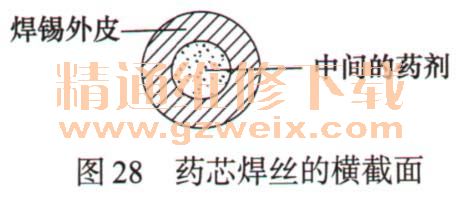
在焊接时,中心的药剂会在加热后放出二氧化碳气,保护高温的焊接面和焊丝不被氧化。
6.3助焊剂
在焊接时,由于电烙铁产生高温,与它接触的电路板表面的金属层和焊丝的表面在高温下极容易被氧化。一旦形成氧化层,就会造成虚焊和电流不畅等问题。这时就需要使用助焊剂来保护焊接过程中不被氧化,如图29所示。
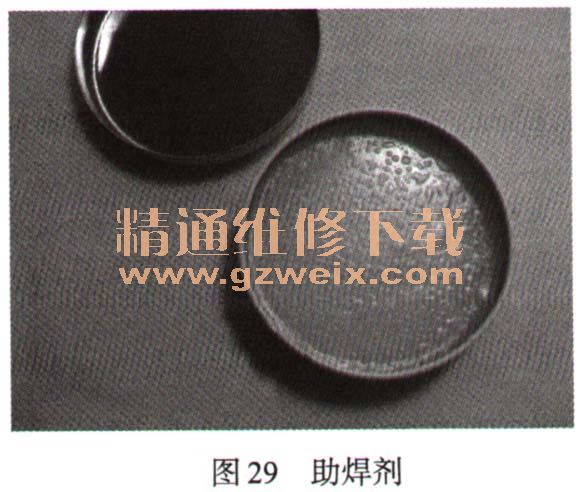
助焊剂的主要成分有有机溶剂、松香树脂、助溶剂、除污剂等。一般用户所用的助焊剂主要是松香。
6.4吸锡器
在拆卸已焊接的元件时,吸锡器起着关键的作用,如图30所示。
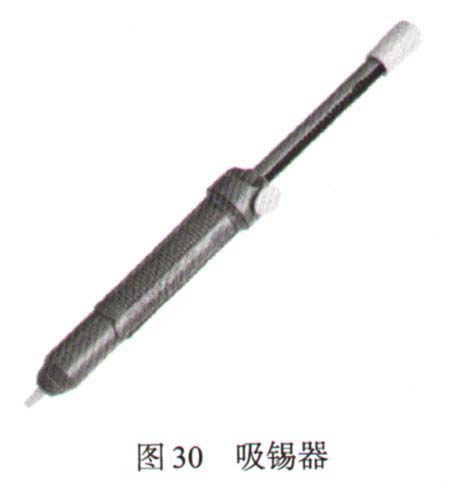
吸锡器的构成与注射器相似,由吸嘴、针筒、活塞组成。针筒上有一个控制活塞的按钮,按下活塞后,将吸嘴对准要熔化的焊锡,按下活塞按钮,活塞快速弹出,针筒中迅速形成真空,熔化的焊锡会在空气流动的带动下,一下被吸到针筒中,如图31所示。
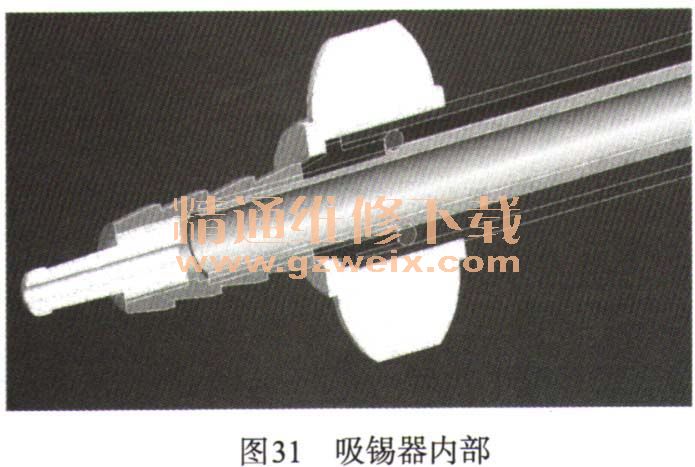
6.5调温台
调温台是电烙铁的供电控制设备,可以很方便地控制电烙铁的温度,如图32所示。
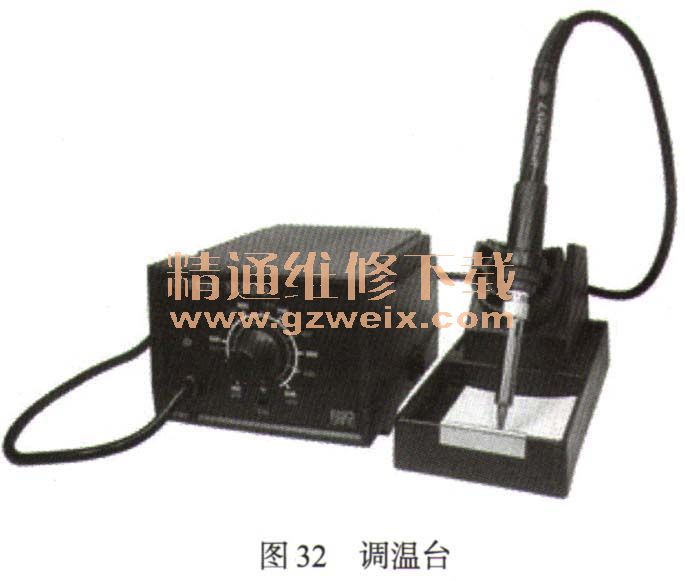
电烙铁使用时,不能长时间地加热,否则会造成表面氧化、寿命降低等不良的后果。使用调温台可以控制电烙铁的输出功率、温度,以便于多次焊接。
6.6电烙铁的使用方法
正确的电烙铁的拿法有正握法、反握法和笔握法,最常用的是笔握法,如图33所示。
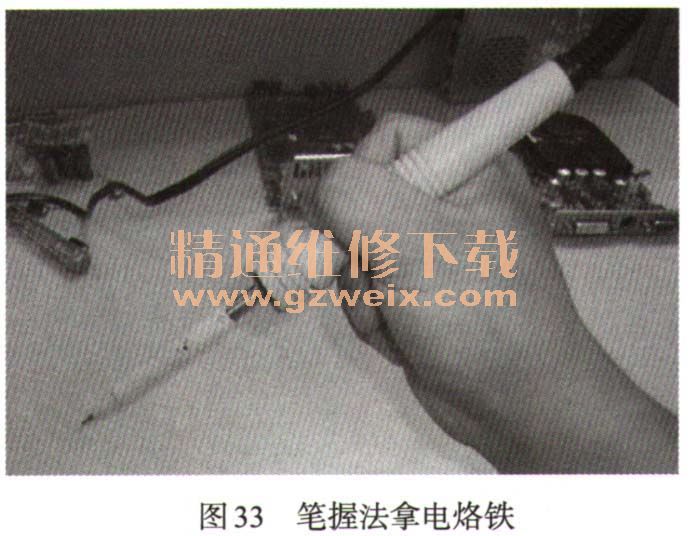
1.电路板和元器件的焊接方法
1)准备好焊接设备和焊接材料。
2)如果电路板和元器件引脚上有氧化层或污垢,先用松香酒精溶液清洗掉氧化层和污垢。也可用助焊剂涂抹氧化层。
3)如果电烙铁头上氧化严重,可以用钢锉等将烙铁头上的氧化层磨掉。
4)电烙铁插电预热。
5)将电路板和元器件固定好。
6)电烙铁头以45°~60°角接触电路板和元器件的引脚(即焊点)进行预热,需要1~2秒。
7)将焊丝插在焊点上1~2秒的时间,焊丝会熔化在焊点上,撤去焊丝。
8)等焊丝均匀地熔化在焊点上,就撤去电烙铁,让焊点的焊锡自然冷却。
9)等焊锡冷却凝固后,用鸭嘴钳剪掉多余的元件引脚。
10)断电后用电烙铁的余温,蘸一点焊锡在烙铁头上,防止烙铁头氧化,如图34所示。
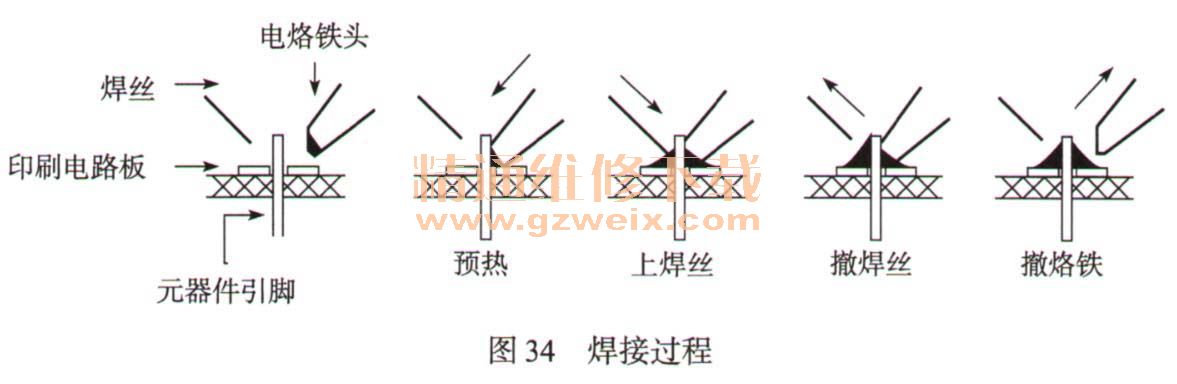
在这个过程中需要注意的是,不要把烙铁头直接戳在电路板没有铜皮的地方。因为印刷电路板没有铜皮的地方是PCB板,是电塑料纤维做成的,直接接触高温的话,会被烧焦甚至烧穿。也不要用烙铁头直接接触助焊剂,会把助焊剂烧黑,影响美观。焊接过程如图35所示。
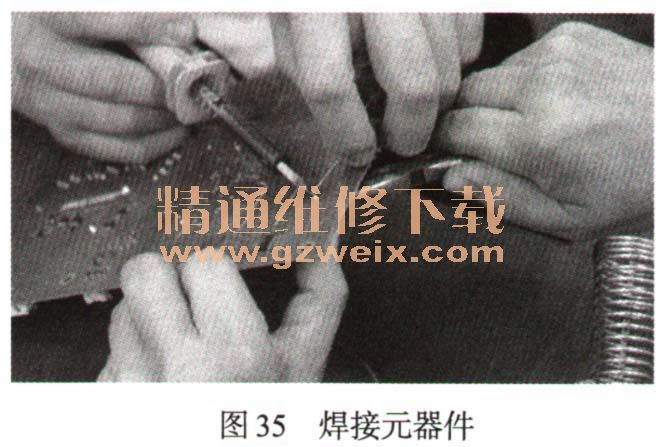
上一页 [1] [2] [3] [4] [5] [6] [7] 下一页