解决方案:优化钣喷维修工艺流程
复杂的钣喷维修工艺流程造成了钣喷维修效率低下、维修时间过长的问题,因此在整个钣喷维修过程中我们需要进行合理的简化,保留其中必须的工艺步骤,消除时间浪费或无用功的部分。现在以中涂底漆整形工艺为例进行简化,如图2所示,笔者将整个工艺流程划分为4个部分:无生产性工时的作业、人工作业工序、设备加工过程和非人工或加工过程。图中第一部分如车辆工件的移入、等待和移出,均属于无生产性工时,也就是无效的动作或过程,该部分未产生任何价值,所以应该尽量消除这部分的时间浪费。
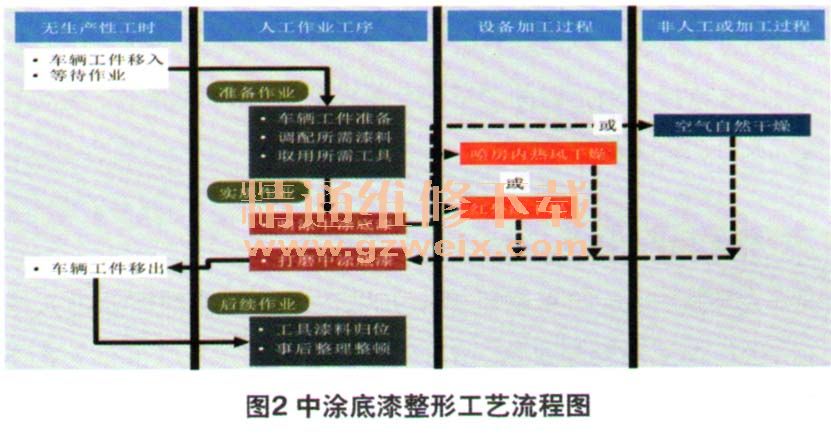
在人工作业工序中包括准备作业、实质作业和后续作业,笔者对这部分进行的详细分析,可参照图3。在这部分维修作业中,笔者建议在准备作业时,将该工序所需的工具设备及物料一次性拿到维修工位,包括取用所需漆料与工具、混合漆料、底漆倒进
喷枪中、去除油脂、粘尘处理、连接压缩空气及取用打磨材料等,在该过程中应该尽量避免产生多余的动作。实质作业包括喷涂中间平整底漆、打磨中间平整底漆和检查平整度,该过程需要提升维修人员的专业技能和熟练度,以最短的时间按标准完成维修作业。后续作业包括车辆或部件的清洁、设备归位、清洗
喷枪、漆料耗材归位和整理整顿等,这些工作可以避免为下一个维修环节带来不必要的麻烦。
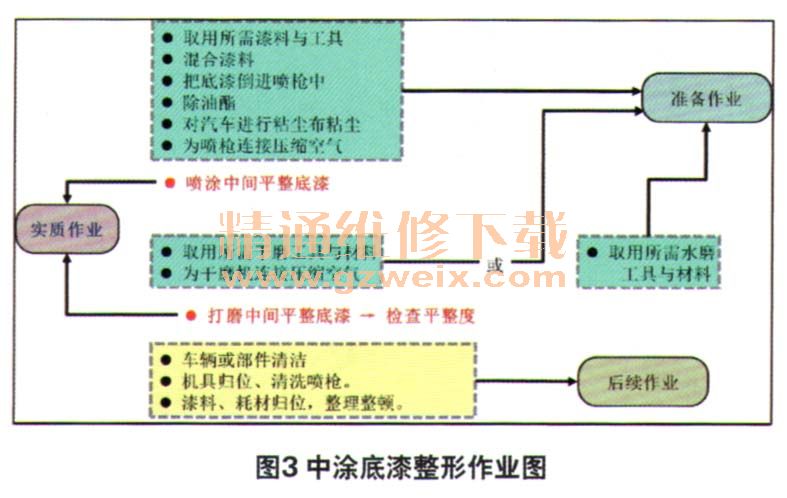
在整个维修过程中,应该尽量提高实质作业的效率,缩短准备作业、后续作业和设备加工过程时间,消除无生产性工时和非人工或加工过程。在相同的工作时间里,有价值的生产时间增多了,也就是直接维修人员的生产率提高了。
除了消除不必要的作业环节和时间浪费,笔者还建议在喷漆车间导入节拍化生产模式,下面仍然以前述那家4S店的小损伤车辆为例,对原先的生产流程进行节拍优化设计如图4所示。
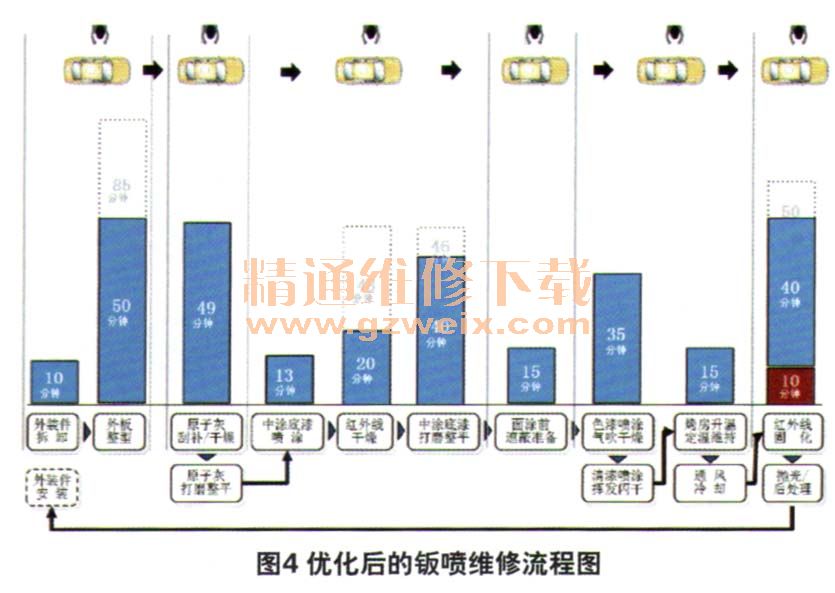
由图4可以看出,在外板整形环节中,将原来的维修时间从85 min缩短至50 min,这可以通过增加高效率的维修设备、提升维修人员的操作技能或者增加维修人员(采用双工位维修)来实现。在中涂底漆环节,将红外线干燥时间从48 min缩短至20 min、打磨时间从46 min缩短至40 min,这样整个中涂底漆环节将变成73 min,可以通过增加短波红外线烤灯、提高干磨效率等方法达到目标。在抛光处理环节,通过提高喷涂质量、保持烤房清洁等手段,将总维修时间控制在50 min之内。由此,我们可以重新对整个喷漆流程进行节拍化设讹如图5所示。
该店每月钣喷入厂台次平均为750台,其中小损伤车辆占70%,所以每天需要维修的小损伤车辆台次为(750/30)×70%=17.5台。每天按照8h工作时间记,则480/17.5≈27 min,也就是每27 min就需要有一辆车完成维修,那么该店的生产节拍就是27 min、以此我们来进行流程的设讯如图5所示,外板整形环节单一工位生产时间是50 min、所以需要有2个工位及2名维修人员同时生产;原子灰处理环节同样需要双人进行生产,并且可安排3台车同时进行;中涂底漆环节和遮蔽环节一共需要88 min,那么可以安排3名维修人员同时维修4辆车,以符合27 min的生产节拍;面漆喷烤环节需要2个烤房同时进行生产;抛光环节需要2人同时完成3辆车的生产。以上的流程设计可以满足目前店内的生产需求,后期如果继续有产能的提升,则需要考虑扩建场地以满足需要。
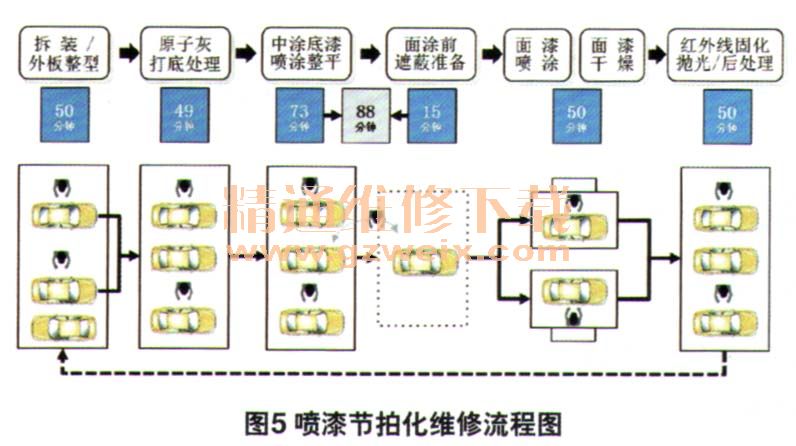
总的来说,优化钣喷业务的工艺流程,不但可以减少车辆维修中时间的浪费和无价值作业,而且通过节拍化的生产模式,各项维修工序由固定的人员进行操作,熟能生巧可以不断提升员工的个人生产率。并且,车辆在各环节流动过程中,下,工序可以对上一工序的作业质量进行检查和监控,保证每个环节都达到质量标准,提升客户的满意度。
上一页 [1] [2] [3]