5.相继增压系统
图39所示是采用相继涡轮增压系统是改善中、低转速扭矩的另一途径。在相继涡轮增压系统中,涡轮和压气机进口处分别装有阀门,以控制
涡轮增压器的投人或退出运行,可以根据柴油机转速和负荷的变化,开动或停止一台或几台增压器。装在涡轮前面的燃气控制阀是以增压空气压力或柴油机转速为控制信号,装在增压器前面的阻风阀是由压力差控制的单向阀。
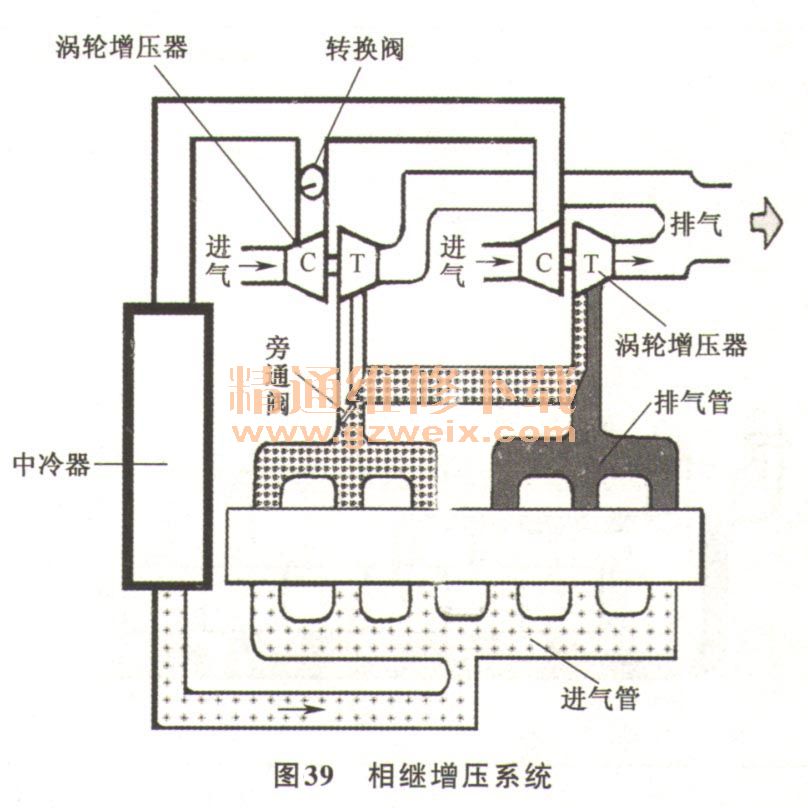
相继增压系统的工作分为三个步骤:
·高转速时碟阀全开,每组气缸的排气分别进入各自的涡轮。
中转速时,碟阀的位置是使每组气缸的排气集中进入各自涡轮中的一个进气口。
·低速时,6个气缸的排气全部进入一个涡轮。
由于采用了相继增压系统,柴油机在中、低转速范围内的性能得到明显改善,柴油机约在标定转速的一半时,也能达到全负荷下的平均有效压力。
6.定压式增压系统(如图40所示)
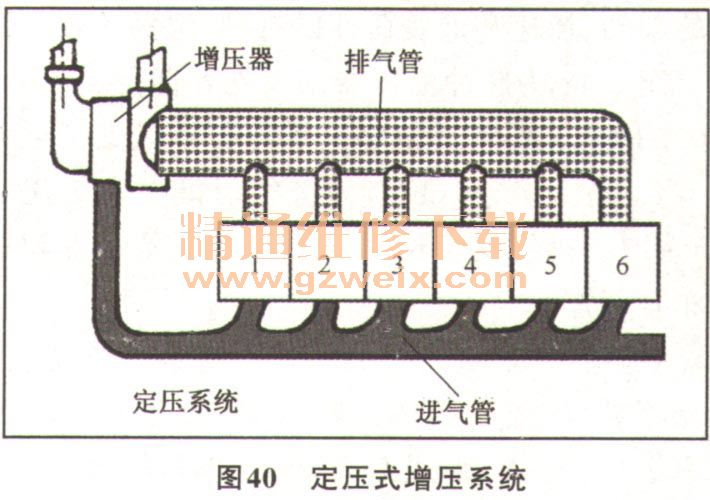
在定压增压系统中,内燃机各缸排气支管都接到一根直径比较大的排气总管,然后和涡轮进口连接。因排气总管容积比较大,实际起到稳压室作用,总管内的气流压力波动很小,涡轮前的燃气压力基本上保持恒定。
定压增压系统涡轮进气压力波动小而且是全周进气,效率高,涡轮受气流激振小,叶片不易断裂,排气管系简单,易于布置和维护。但内燃机排气脉冲能量利用率低,内燃机低速扭矩特性和加速性差。因此,这种增压系统适用于增压压力较高、工况变化范围小的固定式或船用柴油机。
定压增压系统中排气总管应有足够大的容积,以便减少排气压力的波动幅值。排气总管直径dT可按dT =1. 0~1. 2d选取((d为缸径)。
7.脉冲式增压系统
图41所示为脉冲增压系统中内燃机排气支管具有短而细的支管。组织分支原则是将互不影响扫气的两个气缸或三个气缸连接一根排气支管,每一根排气支管端部与涡轮一个进气口连接。整个排气管系的容积较小,排气管内的压力波动和气流动能较大。涡轮处在较大进气压力波动的条件下工作。
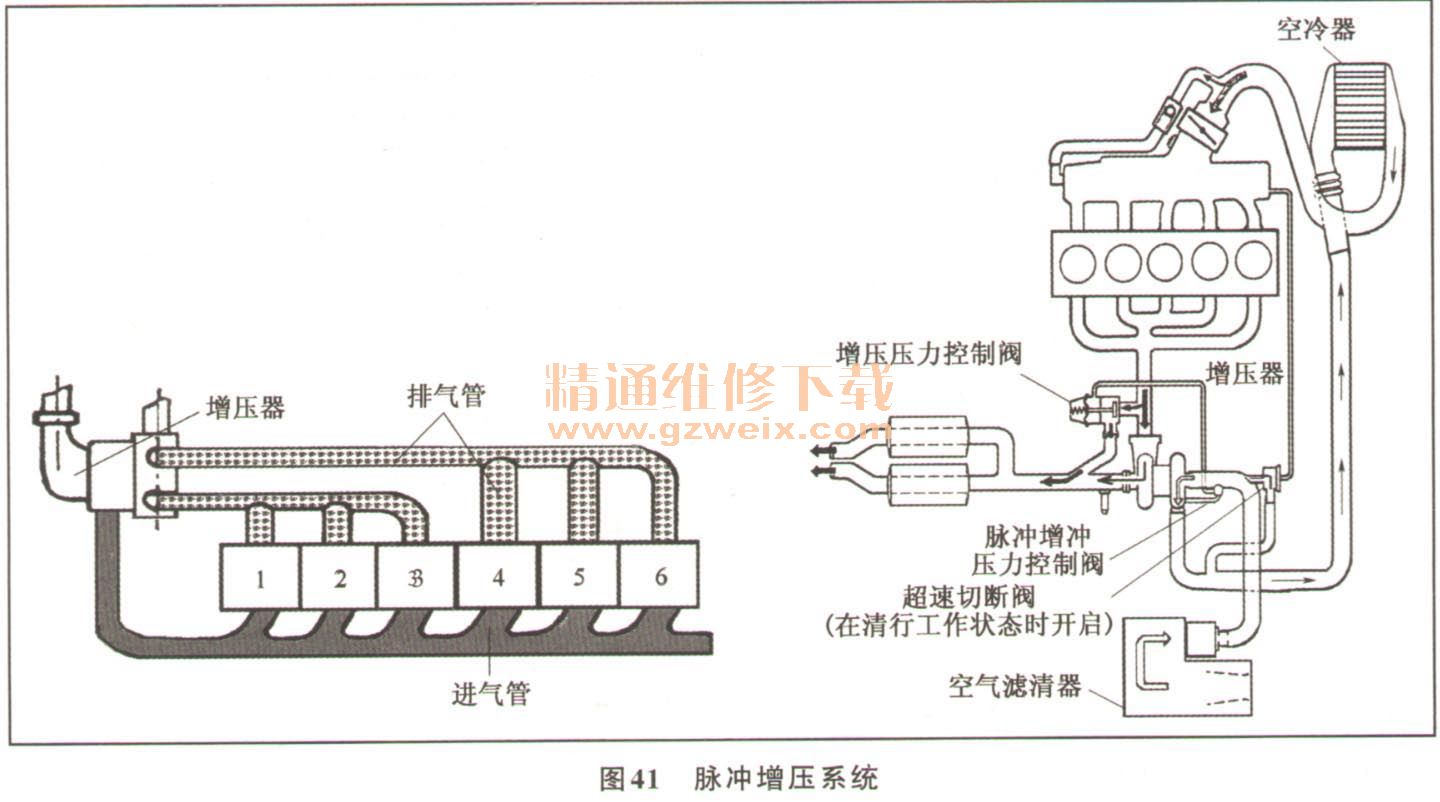
对于缸数正好是3的倍数(3、6、9、12、18缸)的内燃机,能将三个气缸与一根排气支管连接而不影响气缸扫气,常称为“三脉冲系统”,但对于缸数不是3的整数倍如4、8、10、16、20等多缸内燃机,为了不影响气缸扫气,只能两个气缸与一根排气支管连接,则称为“双脉冲系统”。
脉冲增压系统中内燃机排气脉冲能量利用率高,有利于内燃机气缸排气和扫气,这对内燃机的起动、加速和低负荷性能有利,但涡轮效率低,排气管系复杂。
图42为脉冲增压器排气支管直径dT可按dT=0.33~0. 40d(d为缸径),也可按排气支管截面积Fp =1. 1~1. 3 Fmax(Fma、为排气门最大有效流通面积)选取。排气支管长度要根据增压器在发动机上的布置而定。
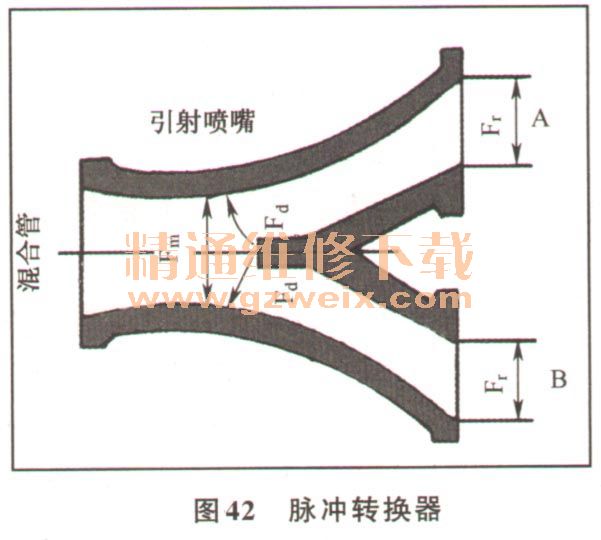
各缸排气通过较长的支管与脉冲转换器[由引射器喷嘴(收缩段喷嘴)、混合管、扩压管(段)和稳压室组成]相连,脉冲转换器再与涡轮进口连接。脉冲转换器连接柴油机一个气缸或两个排气不相干扰的气缸引出的排气支管A和B。当A支管中某缸排出废气经过引射喷嘴时,废气脉冲压力能转变为动能。废气在较低压力下流速提高,此时B管所接的气缸处于扫气阶段,因为背压较低,就和A管出来的废气一起流入混合管,所以不影响该气缸的扫气条件,然后共同进入扩压管中转变为压力能,再经稳压室使压力趋于稳定的气流进入涡轮。因此,脉冲转换器在能量传递效率方面优于定压增压系统,在涡轮效率方面优于脉冲增压系统。这种增压系统用于气缸数目不是3的倍数,如4缸、8缸、16缸等的涡轮增压内燃机。
在实际应用中,往往采用省略扩压管和稳压室并缩短混合管的简化脉冲转换器。
脉冲转换器的结构尺寸关系大致为:排气管截面积FR=(0.95~1.05)fmax(fma、为排气门最大开启面积)或FR=(0.125~0.16)A(A为活塞面积);引射喷嘴出口面积Fn=(0.50×1. 00)×FR;混合管面积FM =(0. 45~0. 65) YFR;或Fm =(0. 45~0. 65)X2FR;涡轮一个喷嘴组的出口面积fN=(0. 50~0. 75)FR。
上一页 [1] [2] [3] [4] [5] [6] [7] [8] [9] [10] 下一页