补偿活塞的这个供给油路又分出2部分:一部分流向4-5-6离合器的补偿活塞腔;另一部分则流向回流油路,此回流油路经过离合器控制阀的调节,最终给离合器的作用活塞提供作用油压(图10中的蓝色部分)。回流油路是从补偿供给油路中分出的,流经一个节流孔后形成。当离合器在处于释放状态时,离合器作用活塞腔里并非是空的,它通过回流油路进行油压的预充。它的设计目的是为了在离合器接到作用命令后,离合器摩擦片能更快速地结合,也就是为了提高换挡速度,以和
双离合变速器竞争(
双离合变速器由于使用2个离合器分别控制1、 3、5奇数挡和2、 4、 6偶数挡,当变速器位于一个挡位时,它的下一挡位已经准备好了,因此它的换挡速度很快)。
图10中绿色的补偿供给油路在进入离合器的补偿活塞腔中,能和回位弹簧一起来推动离合器的作用活塞,因此补偿供给油路的设计能比单独的回位弹簧更快地使离合器释放。而从补偿供给油路分流出来的回流油路(通过离合器预充油压),则能使离合器的结合更快。因此变速器控制单元可以对离合器的动作进行更快和更精确的控制,从而产生更平稳的重叠换挡控制。
现在再来看一下这个补偿油路是如何实现上述第4个功能的(蓄压功能)。从图10可以看到,4-5-6离合器调压阀将油压调节后输向离合器的作用活塞(图中蓝色部分),但是它同时还控制着一个泄压孔,这个泄压孔调节着回流油路的泄压大小。因此当离合器开始作用时,离合器调压阀同时控制着离合器的作用油路和平衡活塞上的补偿油路,当作用油压增加时,补偿油路也会相应地增加。这样设计的一个功效是增加换挡过程中离合器结合的缓冲性能,相当于一个额外的蓄压器,以增加换挡的平稳性。
通过以上的分析可以看到,如果补偿供给油路工作不正常,就会导致变速器的换挡故障,包括以下这些故障现象:换挡冲击;两挡同时作用(运动干涉),耸车;换挡时出现空挡,发动机瞬时空转;降挡冲击;离合器片烧毁;变速器过热。
与此补偿油路相关的故障是常见的问题,因此在故障诊断和分析故障根源的过程中,需要有一个整体的思路。首先要检查图11~15中的离合器各部件,尤其是补偿活塞的状态,这也是最容易检查的部分。但即便看到烧毁的离合器片,也不能止步于此,因为离合器烧毁往往是故障的表现而非根本原因,这就需要继续检查离合器补偿油路在输入轴上的供给通道。如图15所示,4-5-6离合器的补偿供给油压是从输入轴传来的,输入轴上的密封圈如果损坏,会使补偿供给油压从这里泄漏,从而使离合器片在半打滑状态中烧毁。最后才涉及对阀体中油路的检查。
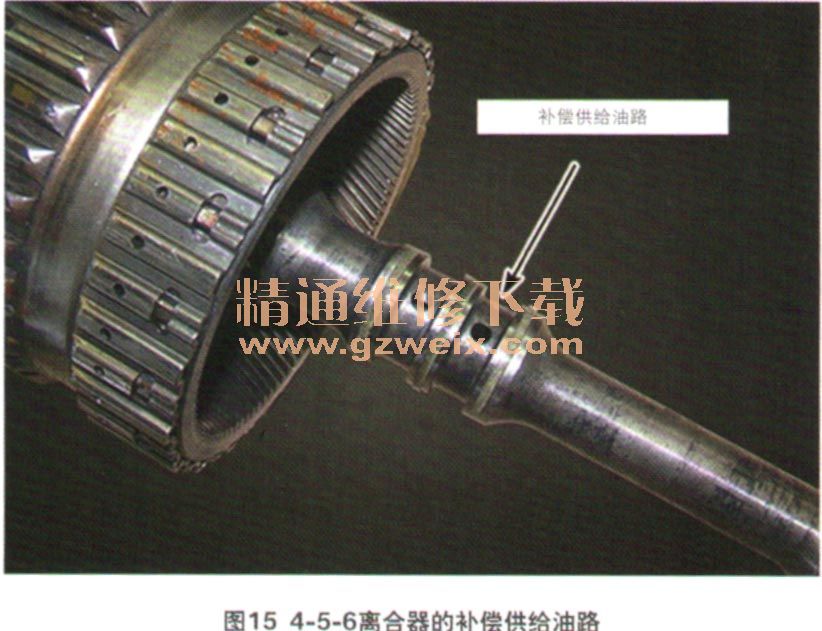
补偿供给油压还通过一个节流孔对变速器后壳上的杯士进行润滑。如果发现任何关于润滑失效或变速器过热的现象,也需要对上述的补偿供给油路进行检查。
在维修新款的6挡或以上变速器时,对离合器故障的分析需要有一种更新的思路。普通的思路往往是检查离合器作用油路的方面,比如离合器鼓是否开裂,作用活塞是否正常,阀体中的离合器调压阀或阀孔及相干油路是否磨损等。但是在6挡或以上的新款变速器中,我们还需要检查平衡/补偿油路的相关油路,因为平彻补偿油路的工作正常与否直接与换挡品质相关。
在通用6挡的变速器上没有油压的测量口可供油压的分析诊断,因此特别需要检查阀体中的补偿供给调压阀(图10和图16)。此阀的设计是专门用来调节活塞的补偿供给油压的,它的运动频繁程度很高,始终处于不停的往复振动中,而且来回运动的行程很小,因此经常可以看到这个阀以及阀孔被磨损。在很多情况下,如果用真空测试法,可以发现此处的阀孔磨损很普遍,这个调压阀的工作状态往往已在临界点附近或以下,如要保证对此变速器的维修达到一定的使用寿命,对此阀孔的修复几乎对每一块阀体都是必须的。
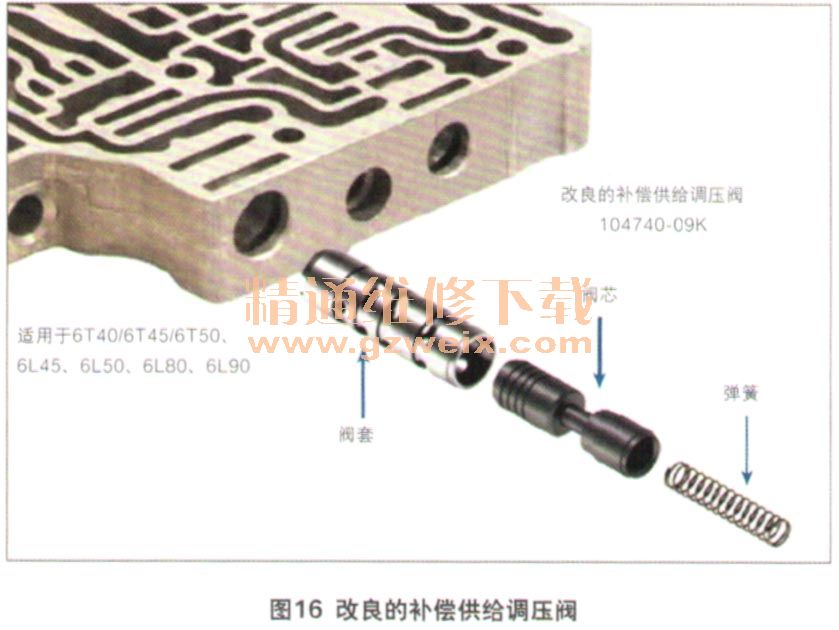
图16中的改良阀是专用于克服原配阀的设计缺陷的,原配阀容易使阀孔出现过早磨损,因此改良阀采用了精密的阀套设计,原来阀孔和阀芯的直接接触现在改为阀套和阀芯之间的接触,这种设计使阀体在报废前将不会在此处因磨损而失效。此处的修复只要直接进行改良阀的更换即可,无需进行铰孔等机械加工。
在维修通用系列的6挡或更新款的变速器时,需要关注对补偿供给油路的检查,这样会使返修率降低,并且变速器维修的质量也更好了。
上一页 [1] [2]