伸缩式吊臂是随车起重机起重作业部分的重要部件,其重量一般占整机的13%~20%。因此通过优化吊臂截面结构,选择合理的截面形状,可以降低吊臂的重量,是提高吊臂的强度、刚度和整体性能的主要途径。通过运用有限元软件对结构实现优化设计是比较成熟的技术。
吊臂为四边形截面一般由上下盖板和腹板焊接而成,制造工艺简单,具有良好的抗弯和抗扭等优点,但是这种截面不能充分发挥材料更高强度的承载能力,各吊臂间需要设附加支承来很好地传递扭矩和横向力,局部稳定性较差,通常在腹板上间隔一定距离设置纵向筋,或在腹板的外侧设置斜向筋,来增强吊臂的抗弯曲能力。五边形与六边形截面的腹板和下盖板的实际宽度较小,有利于提高吊臂局部的抗失稳能力。前后滑块均支承在四角处,且能较好地传递结构的扭矩与横向力,伸缩臂各板之间不产生局部弯曲,因此这两种截面的伸缩吊臂能较好地发挥材料机械性能。
由以上的受力分析可知,起重机伸缩吊臂是以受弯为主的双向压弯构件。吊臂优化设计方案的确定是将吊臂截面尺寸进行调整,各个吊臂臂头支撑结构调整减重,以及各个贴板形状调整减重。
在ANSYS环境下进行结构的优化设计,必须确定结构的优化变量,主要有设计变量、状态变量及目标函数。由于伸缩吊臂的长度是由起重机作业范围确定的,不能改变,因而吊臂的优化设计归结为其截面的参数优化设计问题,优化设计变量应是截面参数,即截面形状和壁厚等。状态变量是设计变量的函数,制约着设计变量的取值。目标函数定为吊臂的重量,最终目的是使重量最轻。对于升湘机械公司的随车起重机伸缩吊臂结构的优化设计,我们主要考虑两种比较重要的工况:基本臂工况,全伸臂工况。具体分析可见图1~8。
根据ANSYS计算及市场反馈的相关信息,综合调整各个贴板的板厚、尺寸、位置及焊接方式。所有吊臂均采用HG70钢。最终确定了优化方案。在基本臂长度为4500 rnm的前提下,使得升湘机械公司吊臂与目前国内同等工作参数的吊臂系统重量更轻,相对于优化前的吊臂减重80 kg,效果是十分明显的。
计算得基本臂的重量约为450. 5 kg,较优化前减重了约35 kg;二节臂的重量约为328 kg,较优化前减重了约19 kg;三节臂的重量约为235 kg,较优化前减重了约15 kg;四节臂的重量约为189 kg,较优化前减重了约11 kg。
2 伸缩机构设计
吊臂伸缩机构采用内置的伸缩系统,经过系统的三维建模,使空间合理、紧凑。各个滑轮均采用全钢滑轮及重载轴承,由于六边形吊臂具有自动对中能力,加上前后设置了4处滑块,因此吊臂具有一定的带载伸缩能力,强于市面其他机型。部分滑轮为侧装单边支撑,具有较好的工艺性;油缸支架总成(俗称飞机头)采用长销孔配合的安装结构,定位承载能力强,可维修性明显好于焊接结构。钢丝绳托架采用可转动托架,当吊臂下部遇到障碍物时,能自动转动避开,优于直接焊接在吊臂上的托架。具体见图9、图10。
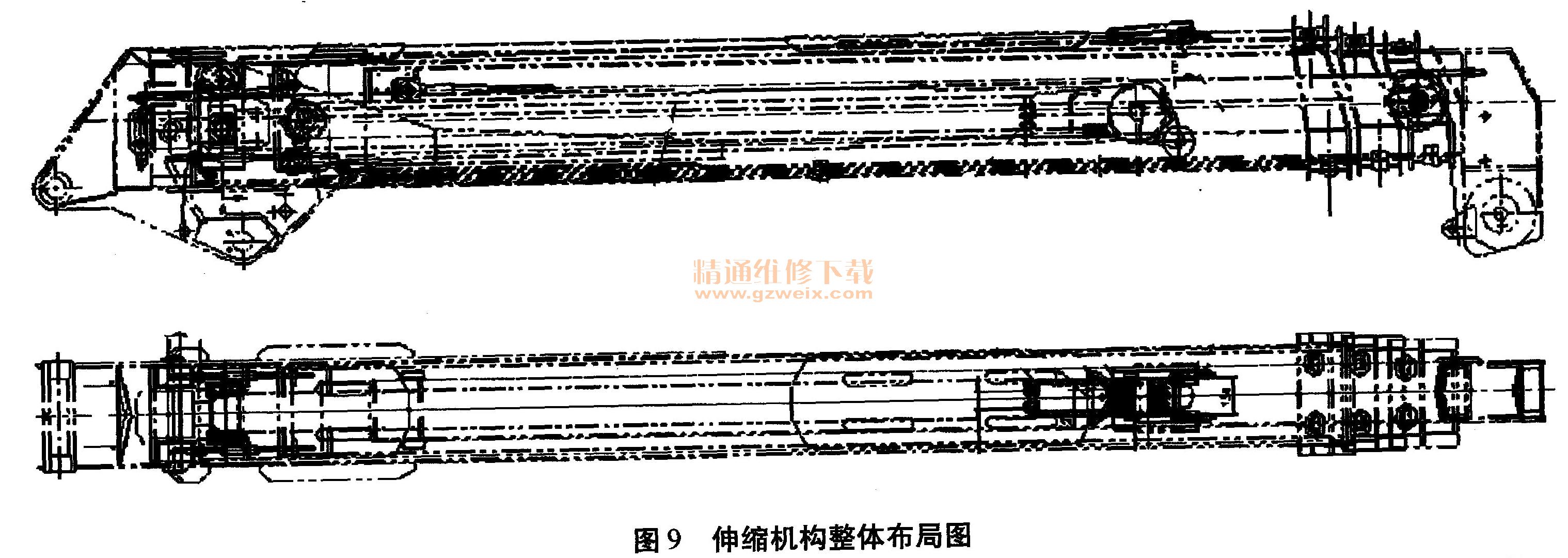
3 .结语
根据改型吊臂的设计成果,常德市鼎城区升湘机械有限责任公司先后对5t三节臂,6. 3 t四节臂,8t四节臂,12t四节臂,9t二节臂进行了系列化的优化设计,均取得上市,取得了良好的经济效益。
上一页 [1] [2]