(五)制订连杆机械加工工艺过程
图3是汽车连杆三维爆炸图,从图中可以看出连杆体和连杆盖这2个零件是通过螺栓联接。
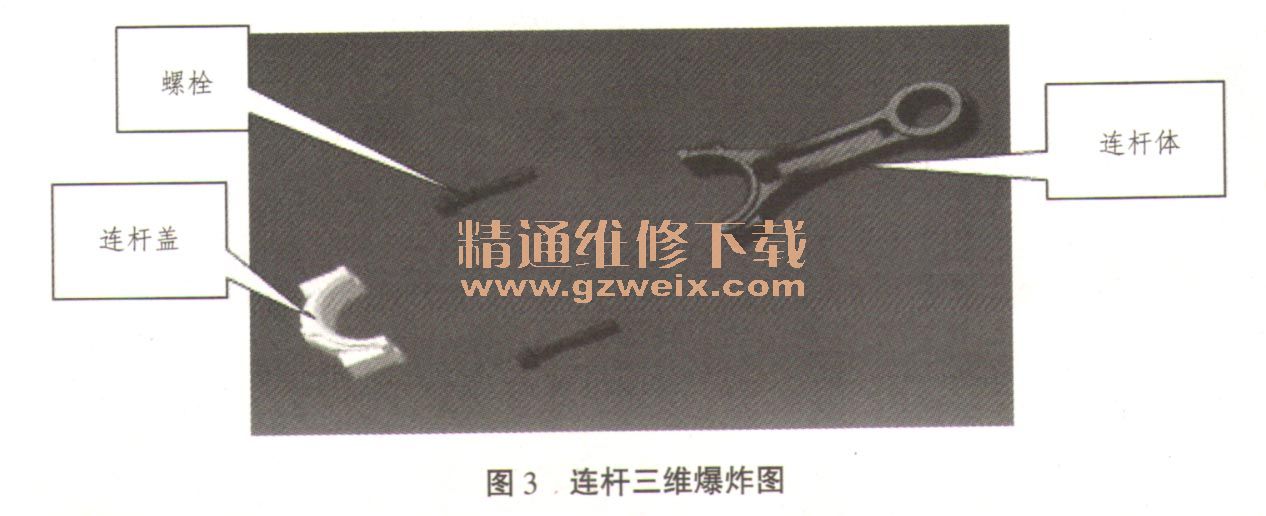
1.工序的安排
为了保证连杆的加工精度,必须考虑以下2个主要因素:
(1)切削力和夹紧力,因为连杆的刚度相对较差,受力容易产生变形。
(2)由于连杆毛坯采用锻造工艺,其本身会产生较大的内应力,并且为了去除毛还件的较大余量,切削过程也会产生很大的残余应力。
所以在对连杆的所有工作表面进行加工时,都应采用三段式加工方法,分别进行粗加工、半精加工和精加工,这种安排方式有利于使后一道工序修正前一道工序所遗留的问题,从而更加保证达到零件所需要的加工精度要求。
根据其加工顺序“先粗后精、先主后次、先面后孔、基面先行”的原则。连杆各主要加工表面的工序安排如下:
两端面:粗铣、精铣、粗磨、精磨;
大头孔:扩孔、粗镗、半精镗、精镗、精钢镗、珩磨;
小头孔:钻孔、扩孔、铰孔、精镗、压入衬套后再精镗。
2.定位基准的选择
定位基准的选择是机械加工中的首要任务,好的定位基准能够切实的保证零件的加工精度。其基本作用是确定零件的相对加工位置,使工件获得高的尺寸精度。按照不同加工过程所使用的定位基准不同,定位基准可分为粗基准和精基准2种。
(1)粗基准的选择原则
①选重要表面为粗基准;
②选不加工表面为粗基准;
③选加工余量小的、较准确的、光洁的、面积较大的毛面做粗基准。
(2)精基准的选择原则
①基准单一原则;
②基准重合原则;
③互为基准原则;
④自为基准原则;
3.连杆基准的选择
连杆的工艺特点是:外形较复杂,不易定位;连杆的大头和小头之间为杆身,其特点是相对刚度较差,容易受力而产生变形,且其本身对各类公差要求及表面粗糙度要求较高。这给连杆机械加工带来了许多困难。为了保证连杆的加工精度,在整个加工过程中应该尽量选择相同的基准面进行加工,这样既避免了多次装夹所产生的误差,又能够避免不同定位基准所导致的附加误差,所以确定使用连杆的大头孔以及小头处的一侧外表面作为基准,既能统一加工基准,同时还能够有效的控制连杆大小头之间的中心距问题。考虑到有些连杆的外形复杂,在加工过程中为了增加可靠性,可适当增加相应的辅助基准,这里不予以展开分析。
(1)粗基准的选择
以连杆的1个端面和大头孔为主要的定位基准,以小头孔处外表面为辅助粗基准。
(2)精基准的选择
考虑要保证零件的加工精度和装夹的准确方便,依据基准重合原则和基准统一原则,以粗加工后的连杆端面和大头孔为主要定位基准,以小头孔处外表面为辅助精基准。
(3)主要表面加工
①连杆大、小头2端面的加工
连杆的大小头端面在后续的大多数工序当中被作为定位基准来使用,所以在制定加工工艺过程时,应首先对这2个端面进行加工,并且根据当时毛坯的锻造余量来选择合适的加工方法,比如铣削或者磨削,随后装配好连杆体和连杆盖,用磨削对该表面进行加工,使2零件的端面处于同一个平面上,且要求其2端面相对于连杆的杆身中心平面对称。
上一页 [1] [2] [3] [4] 下一页