2.制冷系统的部件组成
(1)空调压缩机
压缩机是空调器的心脏,其主要功能就是从吸气阀吸入低温低压的制冷剂气体,将其压缩成高温高压气体后从排气阀排出。传统的空调压缩机有曲轴连杆式、翘板式、斜盘式和旋叶式。若按照传动方式进行分类,则分为两种,一种是带电磁离合器的空调压缩机,另一种是不带电磁离合器的空调压缩机。
1)曲轴连杆式压缩机。曲轴连杆式压缩机是最早应用在汽车空调系统中的压缩机,直到现在仍在大型客车上占据主导地位,在老款的W126奔驰轿车上还能看到。压缩机的进、排气阀同装在一块阀板上,布置在气缸顶部,阀片为环形,进气阀直径较大,装在阀板下方,排气阀直径较小,装在阀板上方。
2)翘板式压缩机。翘板式压缩机的活塞一般为圆周排列,通过连杆、活塞和翘板连接,常见为5缸或7缸。各气缸以轴线为中心,翘板齿轮中心有一钢球定位,并把翘板支承其上沿圆周方向摆动。工作时,翘板一边被向后推,另一边就向前移,每个活塞依次进行压缩和吸气行程。翘板的圆周可以沿输入轴轴线方向前后移动,但不能绕轴线方向转动。
3)
斜盘式压缩机。
斜盘式压缩机是一种轴向往复活塞式压缩机,结构紧凑且排气量大,普遍应用于汽车空调系统。
斜盘式压缩机的结构原理见图2。
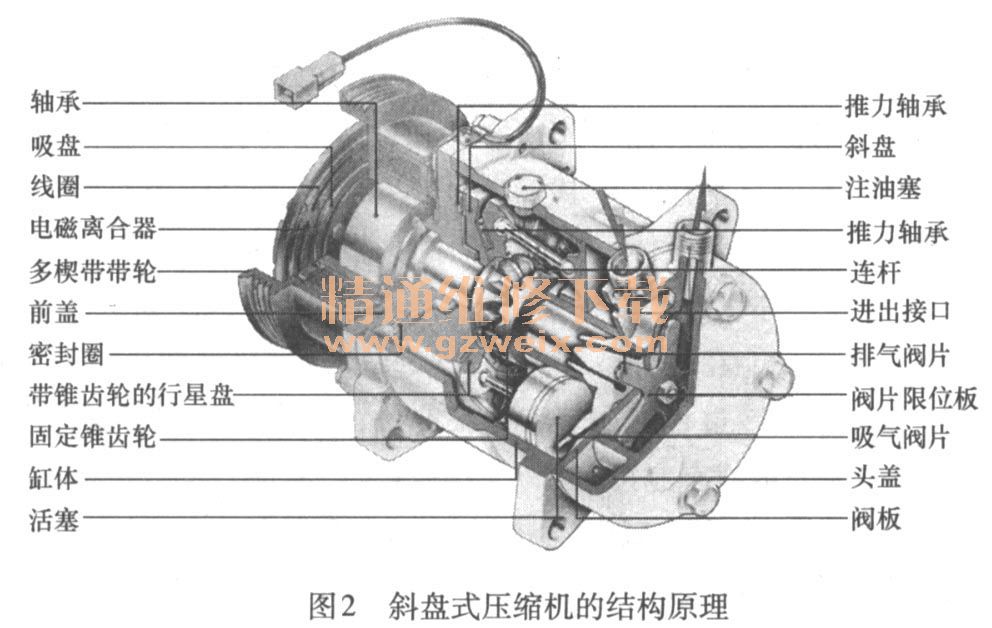
活塞处于前端极限位置是排气的终点,活塞的另一端则处于吸气的终点。当主轴带动斜盘转动时,斜盘驱动活塞做轴向移动,活塞在前后缸体中同时做轴向运动,等于两个活塞做双向运动。斜盘转动一周,前后两个气缸各完成一个循环,相当于两个气缸工作。
4)旋叶式压缩机。旋叶式压缩机是由旋叶式真空泵演变来的,转子的主轴对气缸的圆心有一偏心距,使转子紧贴在气缸内表面的进、排气孔之间,转子上的叶片将气缸分成几个空间,当主轴带动转子转动一周时,这些空间的容积发生扩大一缩小一接近零的循环变化。由于旋叶式压缩机不设进气阀,转子可以高速转动,因此工作效率高,制冷能力强。
5)变排量压缩机。不带电磁离合器的空调压缩机通常都是变排量空调压缩机,这种压缩机目前配置在新款和高档汽车上。变排量空调压缩机按结构划分有摇板型、叶片型和蜗杆型等几种。目前自动空调系统大多使用变排量斜盘式(摇板型)空调压缩机。斜盘将驱动轴的旋转运动方式转换为轴向移动方式,使活塞反复运动。根据不同的结构类型,由5~7个活塞围绕着驱动轴呈圆形排布,每个活塞都配有吸入阀和压力阀,这些阀门在工作时自动打开或关闭,实现对制冷剂的压缩。为了满足复杂的工况要求,活塞的工作行程被设计成可调式,即通过改变斜盘的角度来改变活塞的工作行程。斜盘可沿纵向在一个导轨内移动,活塞行程和制冷剂排量通过改变斜盘的倾斜位置(取决于腔内压力)来确定。变排量空调压缩机的结构原理见图3。
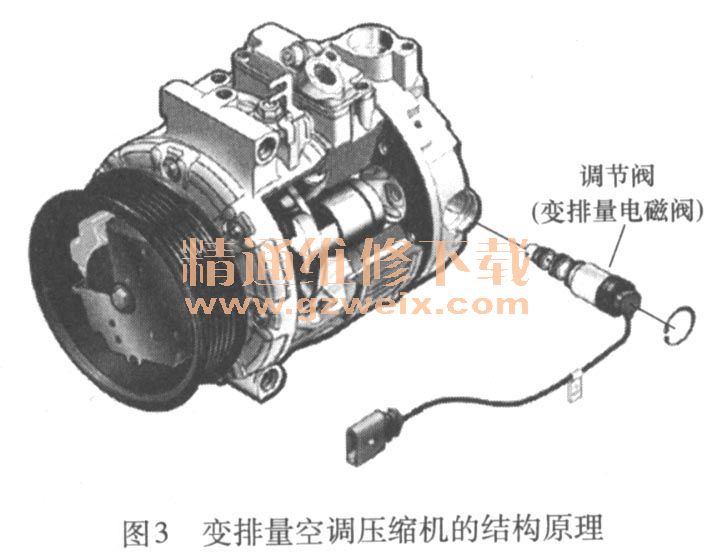
当
蒸发器处于较低的制冷负荷时,斜盘移动到小角度位置,这种工作特点使空调压缩机不必通过减少驱动负荷来产生较高的功率,还可以消除电磁离合器式空调压缩机频率切断的现象。因此,变排量空调压缩机的排量控制是防止
蒸发器结冰的主要因素。为了实现排量可变控制功能,斜盘的角度由每个活塞末端的相对压力控制,即由曲轴箱压力来控制。当制冷负荷需求较高和进行大排量制冷时,曲轴箱压力相对较低,斜盘处于较大倾角位置,控制阀使曲轴箱压力作用到空调压缩机的吸入孔处,因此压力降低;当制冷负荷减小时,控制阀关闭曲轴箱压力作用到空调压缩机的吸入孔的管道,打开曲轴箱压力作用到空调压缩机的排放孔的管道,使压力升高,增大的曲轴箱压力使活塞底部的压力升高,使斜盘移动到小倾角位置,从而减少制冷剂排量。
曲轴箱压力可以通过一个受空调控制模块控制的电磁阀来进行调节,该电磁阀通常称为变排量电磁阀(图4),其工作电流称为占空比工作电流或脉宽调制电流。当制冷负荷较大时,空调控制模块通过变排量电磁阀来减小曲轴箱压力,使压缩机排量增大;当制冷负荷较小时,空调控制模块通过变排量电磁阀来增大曲轴箱压力,使压缩机排量减小。因此,变排量空调压缩机的排量控制取决于两个因素,一是控制阀(通常与变排量电磁阀设为一体)依靠压力进行的位移,二是变排量电磁阀工作电流的占空比。如果变排量电磁阀断电(空调停用或出现故障),那么制冷剂的压缩排量将变得很小(2%),少量的制冷剂循环只用于系统润滑,空调制冷功能则处于失效状态。另外,在以下情况下,变排量压缩机将暂时关闭,以确保系统正常运行和发动机有足够的动力输出:外界温度过低(低于3℃ )、冷却液温度过高(高于118℃ )、制冷剂压力异常(低于200kPa或高于2800kPa)、发动机大负荷工作(强制降挡信号接通或节气门角度接近开全)。
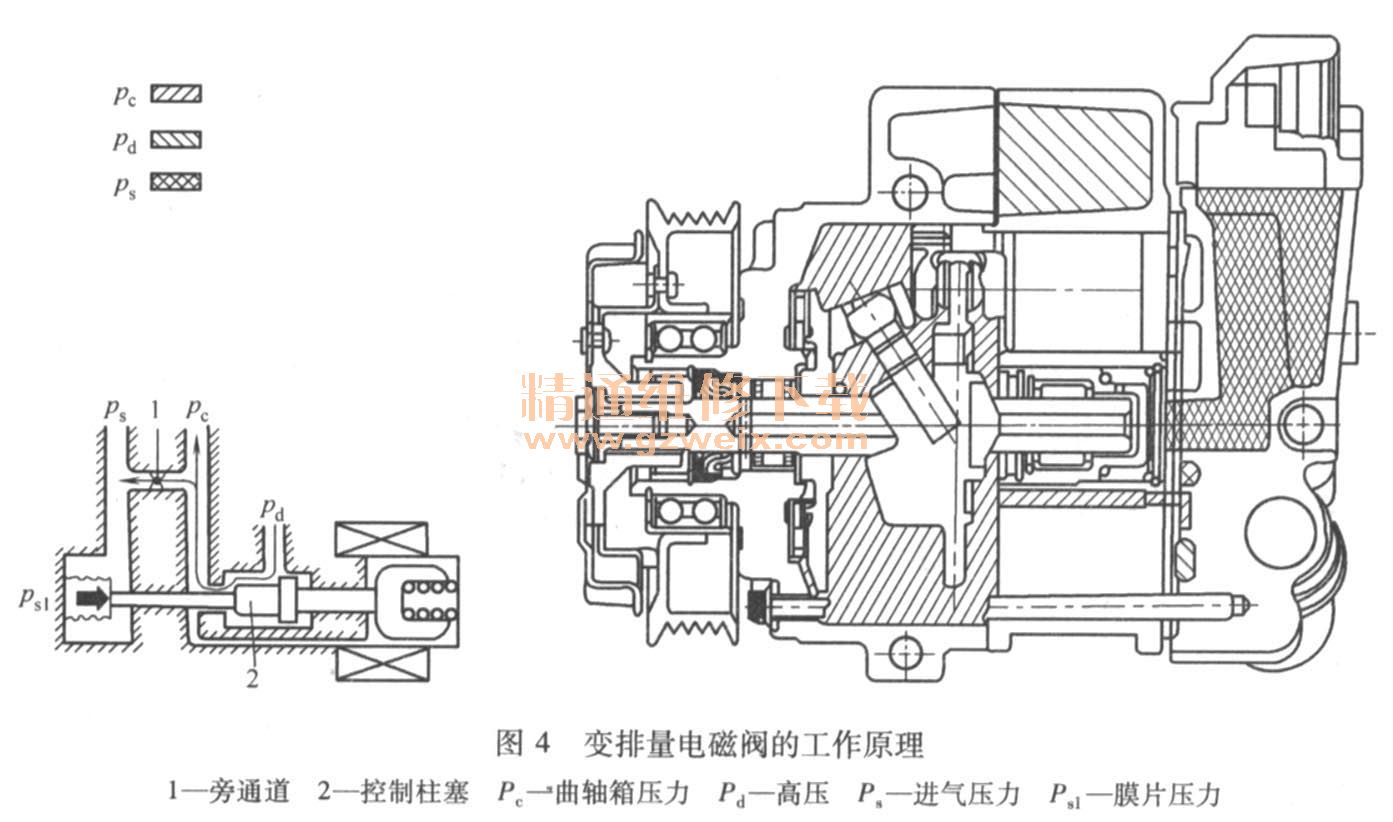
变排量空调压缩机采用常啮合的传动方式,其传动带轮上设有橡胶件,橡胶件不仅起着传动和减振的作用,而且当空调压缩机出现过载或锁死故障时,橡胶件被切断,从而避免出现严重的机械故障。变排量空调压缩机的机械保护装置见图5。
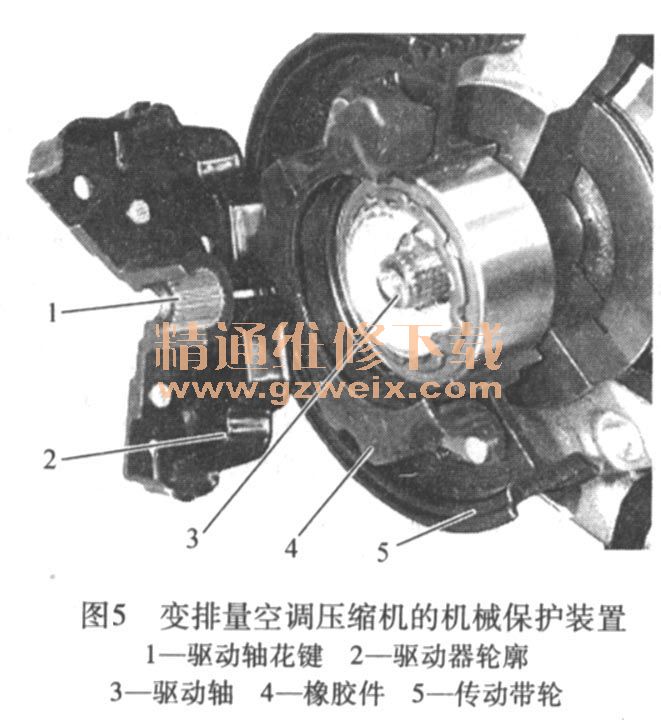
(2)冷凝器
冷凝器用于对空调压缩机排出的高温高压的气态制冷剂进行冷却,通过其金属管壁和翅片将热量释放到大气中去,从而使高温高压的气态制冷剂冷凝成中温高压的液态制冷剂。制冷剂在冷凝器中的放热过程分为三个阶段:过热阶段、两相阶段和过冷阶段。处于过热阶段和过冷阶段的制冷剂为单相状态,而在两相阶段时,制冷剂发生集态变化(凝结),属于一种潜热交换过程。总之,冷凝器中的制冷剂,其大部分热量是在凝结过程中释放出来的。冷凝器的结构型式见图6。
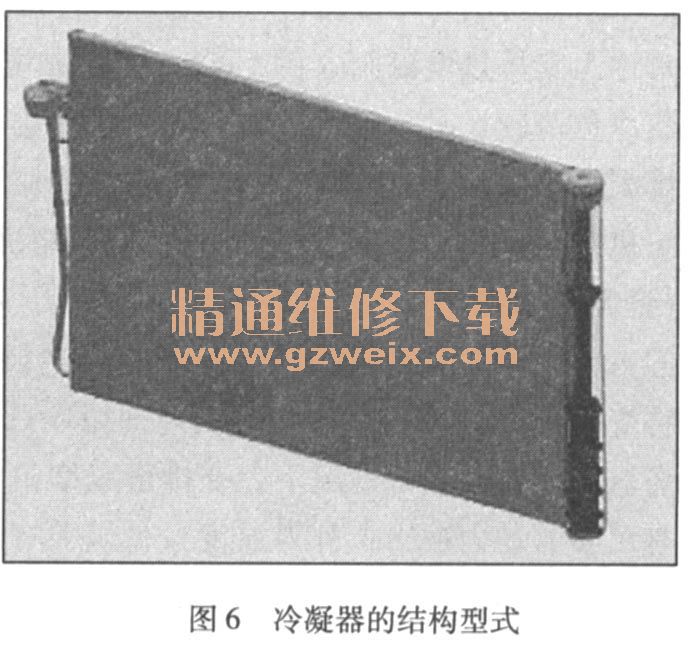
冷凝器本身的散热能力取决本身的结构、尺寸、材料和制作工艺等因素,通风效果则是重要的外因之一。因此,冷凝器通常设置在汽车前部区域,这有利于通过迎面风更好地进行散热。但由于汽车有效空间的限制,冷凝器实际采用的迎风面积往往不够大,因此通过散热风扇进行强制通风是必要的。一般情况下,只要空调制冷模式被启用,电动散热风扇都应运转,而转速的高低取决于制冷剂压力和冷却液温度。
在维修工作中,检查冷凝器的方法一般是查看散热表面是否脏污、堵塞或有油迹,用手触摸散热表面,感觉温度是否均匀。这种简单的检查方法虽然有效,但无法判断冷凝器的热交换效率是否正常,也就是说无法判断内部制冷剂的相变过程。因此,还要结合热力学原理进行检测,即通过测量冷凝器入口端温度、出口端温度和工质压力进行分析,见图7。
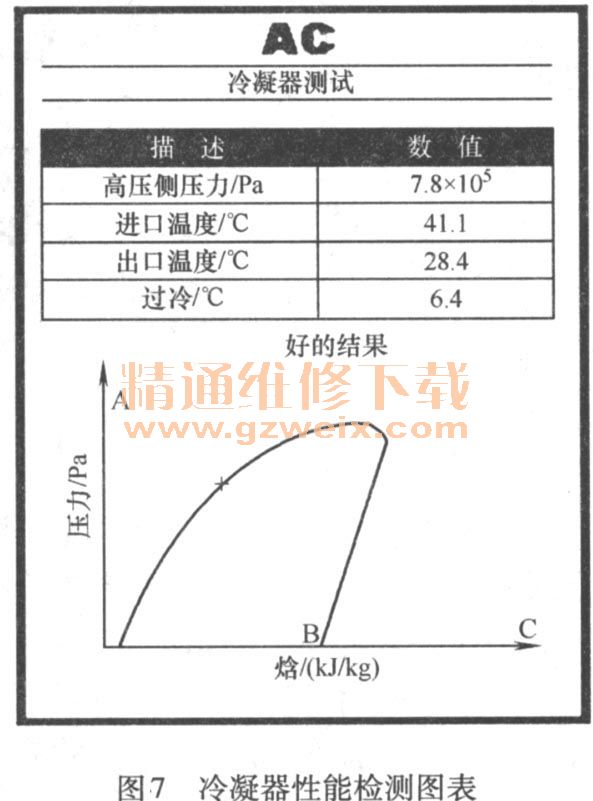
在制冷系统工作过程中,光标会在坐标图中移动。坐标图的横坐标是烩,纵坐标是压力。根据制冷剂相变特性,坐标图分为三个区域:A区表示制冷剂放热充分并以液态离开冷凝器,是正确的结果;B区表示制冷剂放热不充分并以饱和状态离开冷凝器,是不正确的结果;C区表示制冷剂放热不充分并以气态离开冷凝器,是不正确的结果。因此,只有光标在A区移动时,才证明冷凝器性能是正常的。
(3)储液干燥器
膨胀节流装置不同,储液干燥器的安装位置也不同。一般来说,在装配膨胀阀的制冷系统中,冷凝器出口后部设有储液干燥器,从储液干燥器出来的制冷剂已是具有一定冷度的液态制冷剂;在装配节流管的制冷系统中,储液干燥器安装在空调压缩机的低压管路上,这种储液干燥器又称为集液器,可防止液态制冷剂被直接吸入空调压缩机。储液干燥器的结构型式见图8。
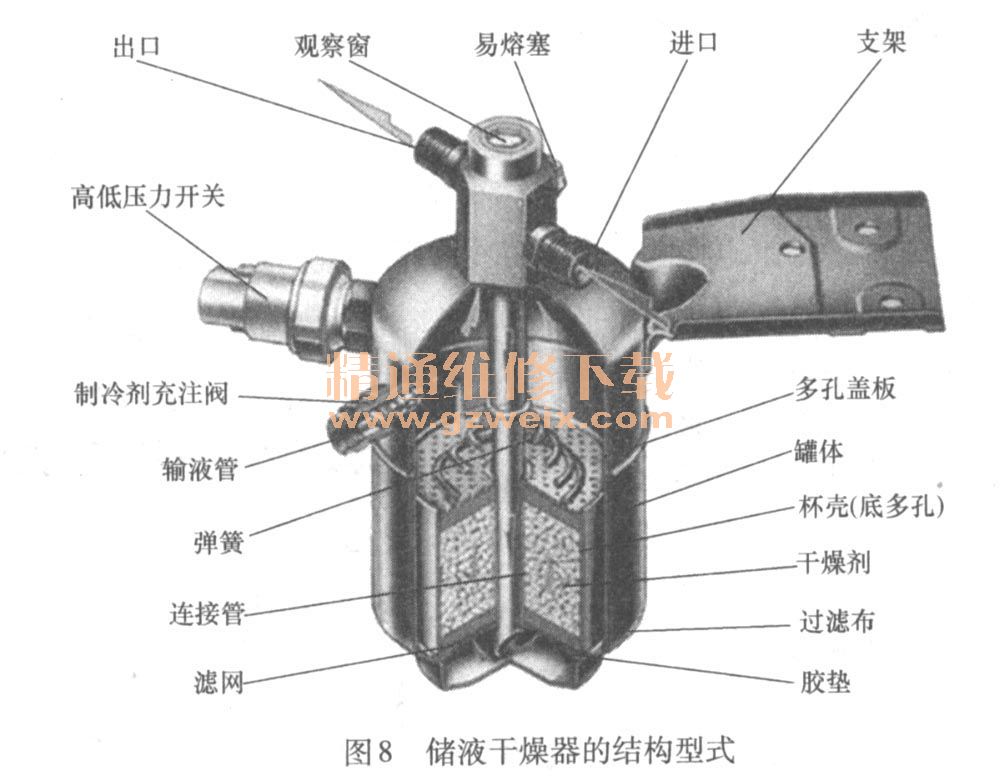
大部分储液干燥器都是一个密封焊死的金属瓶,不可拆卸,里面放有干燥剂、过滤网,装在冷凝器和膨胀阀之间。储液干燥器有过滤杂质、吸收水分、防止堵塞的作用;另外,还可以储存由冷凝器送来的高压液体制冷剂,以适应负荷的大小,随时供给膨胀阀。
储液干燥器是过滤装置,应定期更换,不可维修。储液干燥器常见的故障是吸湿失效和堵塞。如果发现储液干燥器入口与出口之间的温差大于5℃,或出现结霜现象,即说明堵塞,应进行更换处理。
(4)膨胀节流装置
膨胀节流装置用于对高温高压的液态制冷剂进行节流,液态制冷剂因压力降低而雾化,从而吸热、汽化。汽车空调工作环境比家用空调恶劣得多,汽车在行驶过程中,由传动带传动的空调压缩机,其排量不断变化,外界热负荷也不断变化。这就要求膨胀节流装置能够持续进行调节,其参考指标与空调制冷系统相匹配。根据系统的结构及工作方式,膨胀节流装置分为两种:一种是热力膨胀阀,另一种是节流管。
1)热力膨胀阀。热力膨胀阀简称为膨胀阀,它是根据
蒸发器出口制冷剂过热度的大小来调节制冷剂流量的。结构型式和工作原理不同,膨胀阀的工作方式也不同。按照平衡方式进行分类,膨胀阀分为内平衡式和外平衡式两种,其中外平衡式膨胀阀有F型和H型两种结构型式。按照调节方式(静止过热度)进行分类,膨胀阀分为内调式和外调式两种。内调式膨胀阀一般配置在中、小型汽车中,其静止过热度参数(弹簧预紧力)在出厂前已调好,此后在系统维护过程中不必再进行调节,而且装到车上之后,维修人员也无法进行调节。外调式膨胀阀的静止过热度参数由生产厂家调好,在此后的维护过程中还可以根据空调系统的实际运行情况,对外调式膨胀阀进行调整。外调式膨胀阀一般配置在大型豪华客车中,这是因为空调系统的制冷功率大,时间久了容易造成膨胀装置的性能下降。外调式膨胀阀可以通过手动方式进行调整,从而有利于空调制冷系统维护。膨胀阀的结构原理见图9。
上一页 [1] [2] [3] [4] [5] [6] [7] [8] 下一页