(4)小循环的故障隐患
分析
液压系统原理图17和图18,图中实线部分是将油泵的进油口和出油口直接相连,即大众所熟悉的泵阀联体(图21)或泵阀一体,这种结构内部必定存在着油液小循环区域。
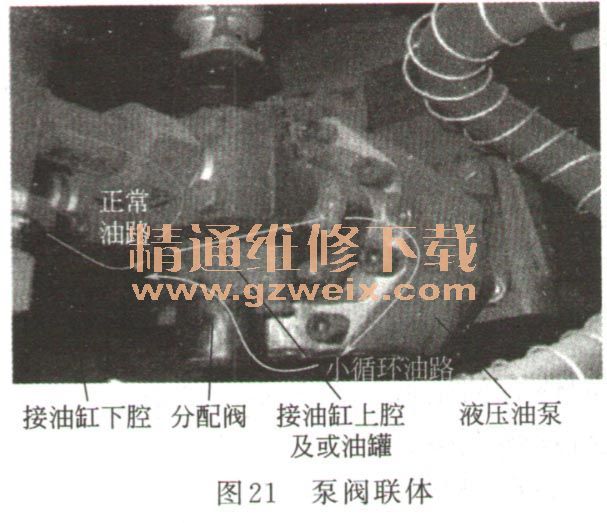
当自卸车处于中停或下降状态时,假设取力器没有及时脱开(客观存在),油泵一直处于运转状态,液压油在油泵的进油口和出油口之间小范围的往返进出,这种油液循环形式,业内一般称作“小循环”,如图21、图22箭头所示区域。
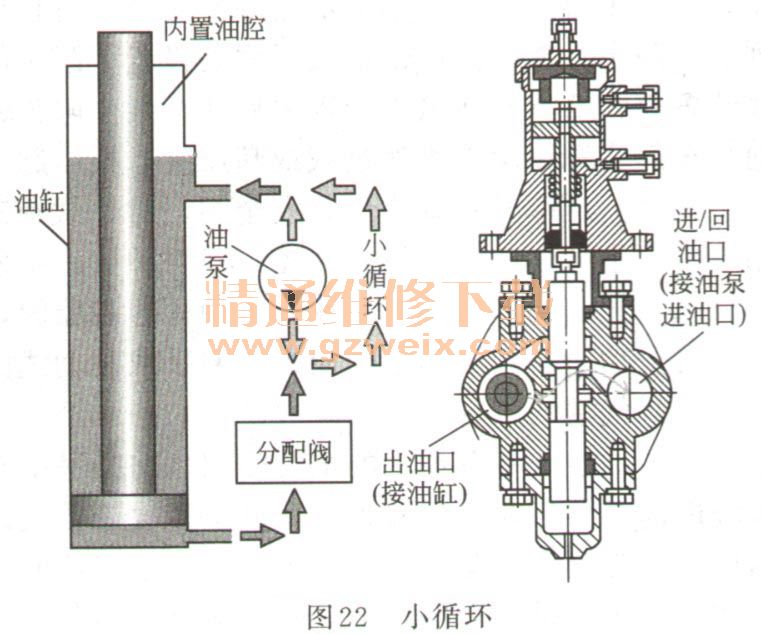
“小循环”主要不利有以下四点。
①液压元件内部摩擦副除了密封和力的传递,还有润滑作用,应保证处于边界润滑状态。当滑动面间的相对运动不能形成必要的润滑条件(边界油膜)时,机械摩擦副将会很快被破坏。“小循环”会迫使油泵内腔局部油液温度急速升高,润滑油膜破裂,出现缺油状态下的干摩擦并造成损伤;继而后续作业时,齿轮与浮动补偿侧板(或轴套)间的摩擦副高速运转时不能建立起有效支撑的边界油膜,在高压油泵内部轴向浮动补偿背压区的压力推动下,极短时间内就会在高温与磨粒磨损综合作用下彻底烧毁元件本身。
②磨损其实就是磨料磨损,干摩擦极易产生金属颗粒污染物,随着油液的流动,当金属颗粒污染物进人其他具有相对运动的接触面之间的缝隙时,轻则引起分配阀阀杆卡滞,造成操控失灵,暂时无法工作;重则损伤密封面的零部件和加速摩擦副间的磨损,引起各种形式的外渗漏和内泄漏,导致元件早期失效。
③局部高温引起液压油变质会严重缩短液压油液的使用寿命。一般
液压系统最适合的温度为40~60℃,在此温度下液压元件的工作效率最高,油液的抗氧化性也处于最佳状态。如果工作温度超过80℃,油液将早期劣化(事实证明,作业温度每升高10℃,油的劣化速度增加2倍);另外,高温还将引起油液赫度降低、润滑性能变差和油膜损坏。
④当局部高温超过密封件的耐热极限时,会造成密封件的炭化失效、密封防护件的软化流动变形,从而引起液压元件内泄漏,导致元件过早报废。因此
液压系统的油液工作温度不宜超过80℃,短时间温升不得超过90℃,一旦超过这一温度,必.须停机冷却或采取增设强制冷却热交换部件。对于液压动力元件的齿轮泵,明确要求局部温度极限一般≤8 5℃。对比
液压系统原理图17~图19,可以看到3者的显著区别在于,液压原理图19中除了所采用的泵阀分体结构不同外,图中还存在实线部分一端连接油泵的出油口、另一端连接着液压油箱的回油口,即在非正常情况下泵出的油液直接流回油箱,彻底杜绝了上述液压油在小范围内往返循环问题。所谓泵阀联体或泵阀一体(图3-21),即油泵与分配阀直接采取刚性连接或将分配阀设计成油泵后盖的一部分的组合体。优势在于结构紧凑,便于布置管路;缺点是散热性稍差、非作业状态下不允许油泵自转(低速运转1min以下,影响不大)。
(5)呼吸孔的隐患
大气中含有的粉尘、管道内的锈粉及密封材料的碎屑等侵人到
液压系统中,将引起运动件卡死、动作失灵、加速元件磨损、降低使用寿命,严重影响系统性能。分配阀为了便于内部阀杆的灵活往复移动,大都设置了呼吸孔,因此也就存在非完全封闭设想在野外恶劣的工况下,阀杆的往复运动、容积的变化,难免会成为矿粉、雨水、灰尘自由的进出通道,自然会出现因颗粒污染物卡住阀芯、阀杆造成液压元件失灵,以及分配阀内部阀杆、弹簧锈蚀,从而缩短分配阀的寿命,并殃及其他液压元件的正常“功效”,最终严重影响到整个
液压系统的可靠性。
与国外某分配阀的对比(图23)可看出,明显的区别在于一个是外置呼吸孔,一个是内置油道。国外某分配阀的优势不仅仅在于阻止了外部污染物的进人,还在于对内部的阀杆、弹簧、密封组件等零部件的润滑或及防锈的作用。

(6)二次举升过程的货箱冲击
在倾卸私滞货物需要二次举升货箱的特殊工况下,如果货箱与车架成某一角度,当操作手控阀3置于“举升位置”时,某些分配阀在切换的过程,阀内部会出现油缸C口、油泵P口、分配阀T口三腔连通的移动工作位置(图24),在货物重力的作用下,货箱会产生不同程度的自行下落(即“点头”现象)。
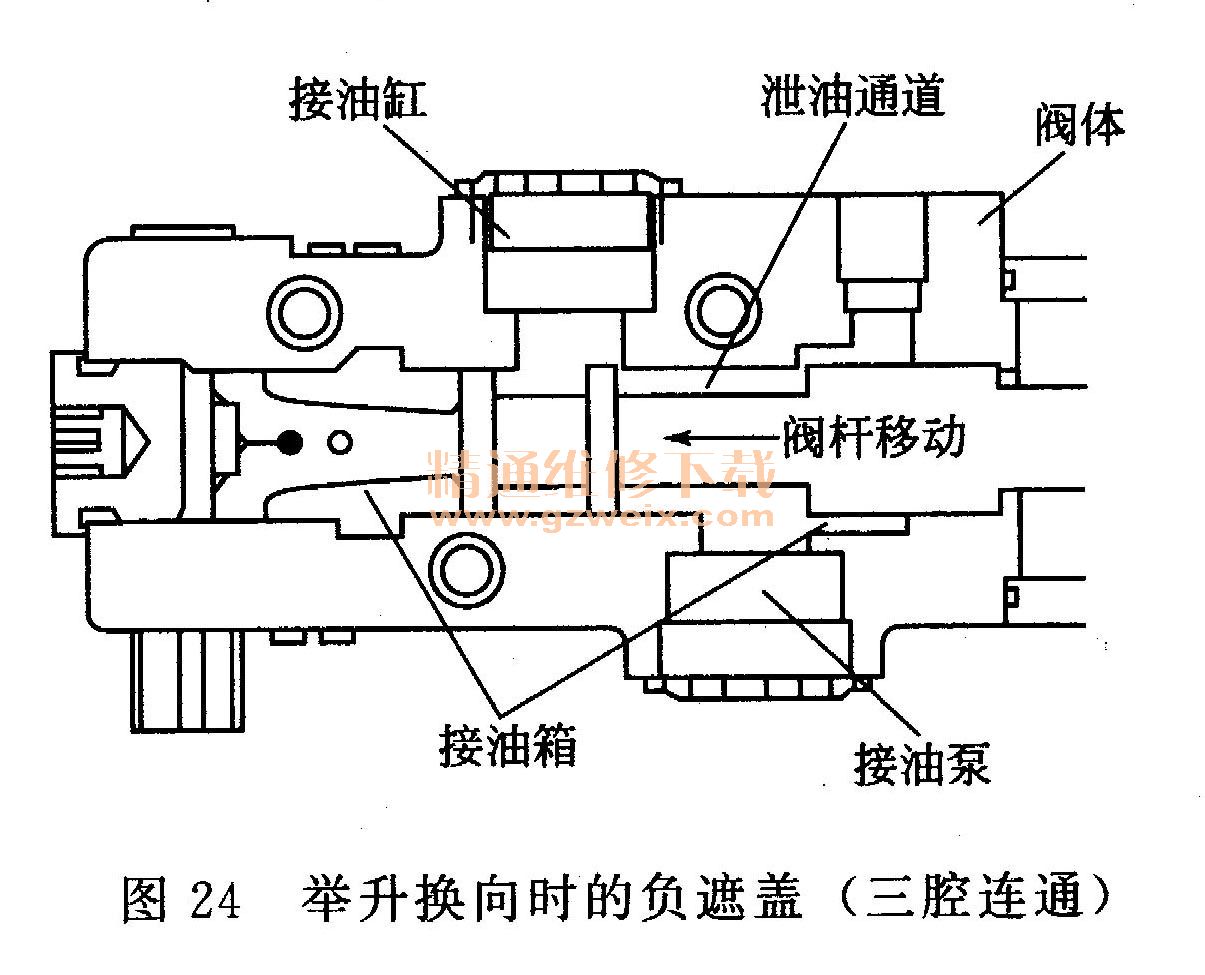
在正常(一次)举升情况下,由于货箱平放在底盘之上,处于水平位置,这一潜在功能缺陷是完全可以忽略不计的;而某些必须要二次举升的工况则不可避免地出现货箱自降点头,重载时甚至出现货箱连同货物冲击汽车底盘,引起驾驶室强烈晃动及上窜的问题,严重威胁驾驶员的安全。
国外某品牌前举升分配阀为了预防分配阀举升切换全过程中,阀杆移动时会将连接油泵出油口的阀内通道关闭(此时油泵与过载阀的油路亦被切断),存在阀内压力瞬间过载的隐患,便将阀杆设计成负遮盖滑阀的形式(图24) 、也是存在三腔连通的状况。虽然在二次举升中也将存在这种现象,但由于有效控制了零件间的位置公差,同时施以极其精密的加工,因只是存在少量的泄漏,并且切换时间极短,在一般情况下货箱的自动点头下落驾驶员是几乎觉察不到的。
上一页 [1] [2] [3] [4] [5] [6] [7] [8] [9] [10] [11] [12] 下一页