(2)堆焊轴孔
将I孔按照孔径方向分为3等分,通过吊装或翻转,优先保证焊接区域处于水平向上位置,其中A区为水平焊接位置,B区为横向焊接位置,如图4所示。焊接区域参数如表2所示。此外,对重度划痕、磨损表面、侧磨损表面(见图2),分别采取不同参数施焊,堆焊厚度视I孔磨损程度决定。
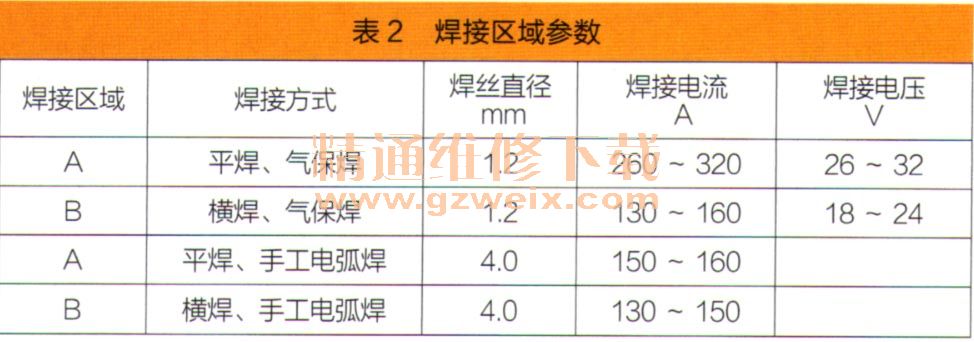
焊接过程中,焊丝沿轴孔方向由外向内施焊。为防止产生未熔合缺陷,焊接时后1道焊缝应压在前1道焊缝的1/2~2/3处。每层厚度控制在2~3mm,焊层之间需进行清渣处理。堆焊结束后,孔径尺寸比标准孔径小10%左右,以便于机加工。轴孔内壁润滑脂孔处直接堆焊,待轴孔完成机加工后用钻头手工钻孔即可。
将斗杆吊至轴套端面平焊位置,堆焊轴孔端面。堆焊前打磨焊缝的起弧端,采用环焊方法由内往外焊接。堆焊后轴孔两端面比标准尺寸厚5~7mm,以保证机加工所需尺寸。焊接过程中,焊缝应保证过渡顺滑,不允许出现流挂、气孔及明显沟壑,以避免影响机加工精度。
(3)加工轴孔
I孔的孔径及端面堆焊完成后,需对其进行机加工,其机加工步骤如下所述。
首先,吊装斗杆并进行预装夹。将堆焊I孔的斗杆吊装至加工中心平台上进行预装夹。此时,先用钢板尺调整II孔、III孔、V孔与加工中心基准面对称度,使其对称度偏差在1mm范围内,确保后续机加工调整精度。
其次,对斗杆进行精确调整并完成定位。使用加工中心的红宝石探头对斗杆进行精确调整,通过红宝石探头测量II孔、III孔端面尺寸并调正斗杆。为确定II孔、III孔中心坐标尺寸,将红宝石探头向上、下、左、右各移动相同距离至A、 B、C、 D点,这4点靠近II孔、III孔端面外边缘且此4点处应光滑无磨痕,如图5所示。
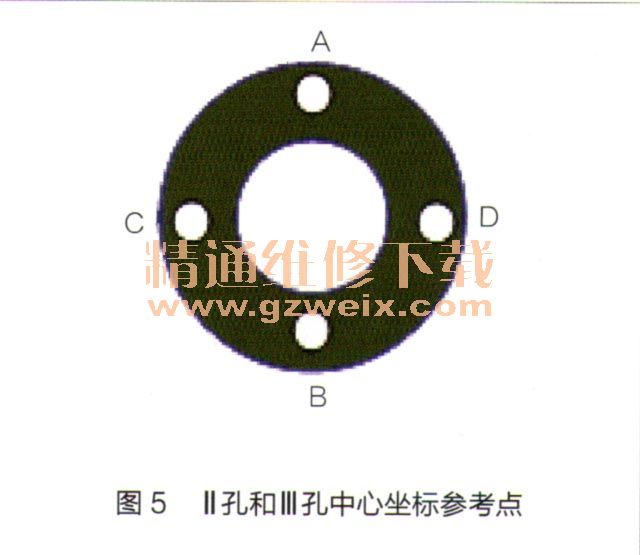
再次,判定I孔加工坐标。设定孔端面此4点处Z坐标轴分别为A、 B、 C、 D,设定斗杆II孔端面坐标为A1、B1、C1、 D1,III孔端面坐标为A2、 B2、 C2、 D2;调整斗杆,保证各坐标点误差小于0.1 mm。测量II孔、III孔、IV孔、V孔各孔中心坐标,通过MDS软件和机床程序判定I孔加工坐标。
最后,按照图纸技术要求对I孔进行加工。加工后补焊孔若有气孔需视气孔状况对其进行适当修整。经检验合格后,该斗杆I孔即完成修复工作。
上一页 [1] [2] [3] 下一页