三、F系列四轮定位的调整
(一)在进行底盘测量前必须注意下列检测条件
1.在车辆上只能安装BMW许可的车轮轮胎组合。
2.胎纹深度符合规定。胎纹深度在整个车桥上的左右轮胎之间允许有最大1~2mm的偏差。
3.轮胎充气压力符合规定(参见车辆上的提示牌)。
4.所有的底盘组件在技术上必须正常。
5.悬架和减震器的状态正常:目检有无断裂等。
6.配备自调标高悬架控制的车辆:拔出供气装置的保险丝,以免往下或往上进行高度调整。
(二)前桥+转向系:下列操作后必须进行底盘测量(如图17所示)
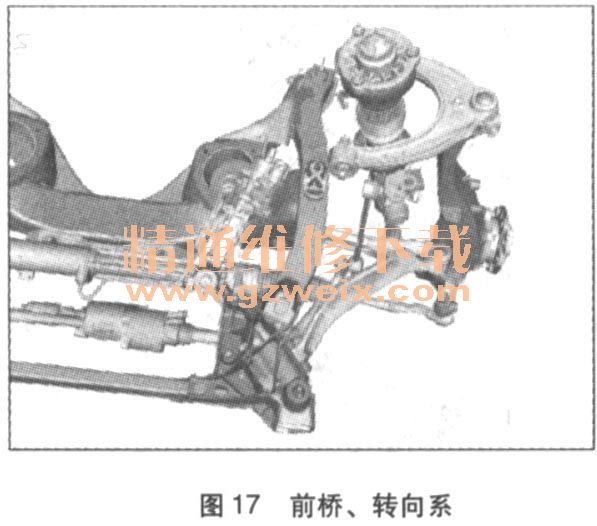
松开下列螺栓连接:
◇转向器安装到前桥架梁上
◇下部横向摆臂安装到前桥架梁上
◇转向横拉杆头安装到转向横拉杆上
更换下列部件:
◇前桥架梁
◇转向器
◇摆动轴承
◇下横向摆臂
◇转向横拉杆头
◇转向拉杆
(三)后桥:下列操作后必须进行底盘测量(如图18所示)
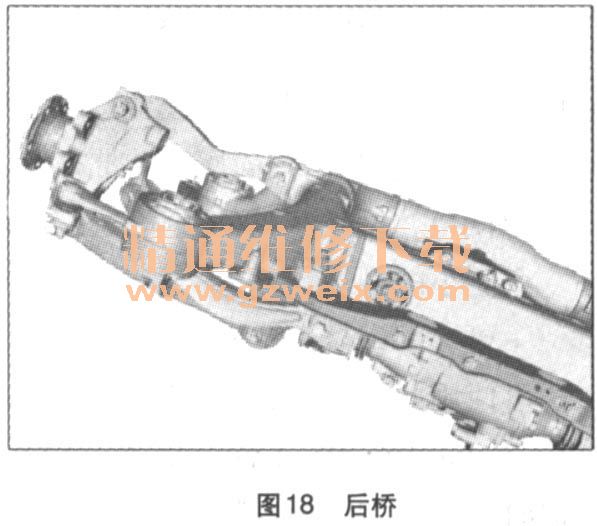
松开下列螺栓连接:
◇前/后摆臂装在后桥架梁上
◇摆臂安装到连接导杆/轮架上
◇导向臂安装到后桥架梁/HSR单元上
◇横向摆臂安装到后桥架梁/轮架上
更换下列部件:
◇后桥架梁
◇HSR执行器
◇横向摆臂
◇摆臂
◇轮架
◇连接导杆
◇横向摆臂
(四)调整后桥
每次转动摆臂上或横向摆臂上的调整螺钉都会引起
车轮外倾角和前束变化,不能再进行单独的
车轮外倾角或前束调整。只能借助下面的图表进行有针对性的
车轮外倾角和前束调整。仅带ACC的车辆,在进行改变行驶轴线的后桥调整后,检查ACC传感器的校准。仅带后桥侧向偏离控制装置的车辆,只能借助BMW诊断和信息系统对后桥进行调整。
图表中的计量单位:〔分〕
根据图19、表1记录的示例值的描述:
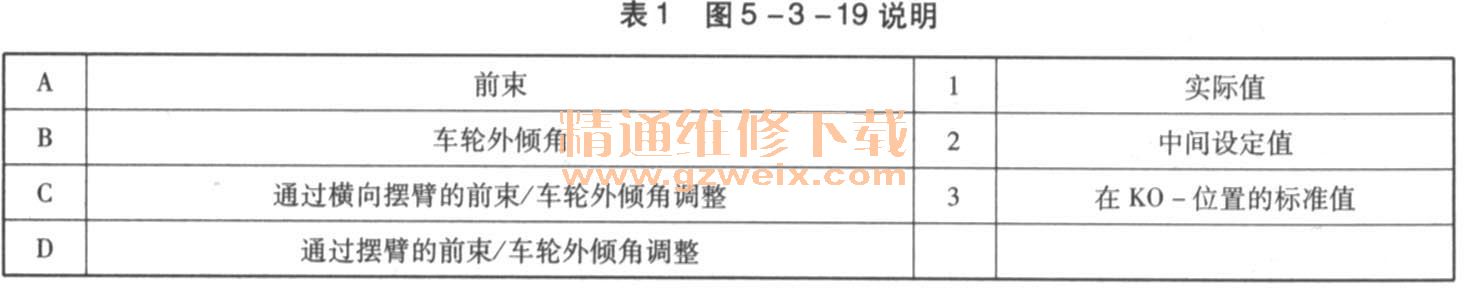
1.在车桥检测台上读取前束/
车轮外倾角的实际值并记录到图表中;
(在本例中,前束一15'、
车轮外倾角一90')
2.通过记录的实际值画“横向摆臂”直线C的平行直线;
3.在“摆臂”直线D上的交点得出前束/
车轮外倾角的中间设定值;
(在例子中:前束一4';
车轮外倾角一108')
4.通过转动横向摆臂的调整螺钉调整中间设定值
◇参见下面描述的工作步骤“横向摆臂上的调整”
5.通过转动摆臂的调整螺钉调整前束/
车轮外倾角的标准值(直线D上的前束/
车轮外倾角值)
◇参见下面描述的工作步骤“摆臂上的调整”
在水位因变测量时,前束-/
车轮外倾角调整的操作步骤(不负载):
图表中的计量单位:[分]
根据图20、表2的调整描述(根据车辆高度的车桥检测/未负载):
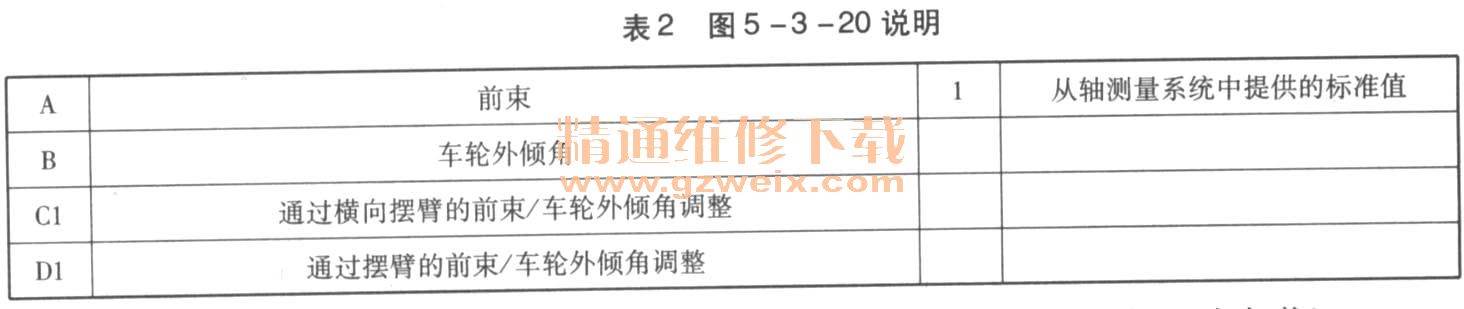
1.在车桥检测台上读取标准值并记录到图表中(本例中前束+12'/
车轮外倾角-78')
2.平行移动直线D和C,使两条直线D1和C1的交点为记录的标准值
3.在车桥检测台上读取前束/
车轮外倾角的实际值并记录到图表中
4.下一步的工作步骤如在结构位置上的调整:
◇通过记录的实际值画“横向摆臂”直线C1的平行直线
◇“摆臂”直线D1上的交点给出前束/
车轮外倾角的中间设定值
◇通过转动横向摆臂的调整螺钉调整中间设定值
◇参见下面描述的工作步骤“横向摆臂上的调整”
◇通过转动摆臂的调整螺钉调整前束/
车轮外倾角的标准值(前束/
车轮外倾角值在直线D1上移动)
◇参见下面描述的工作步骤“摆臂上的调整”
横向摆臂上的调整(如图21所示):
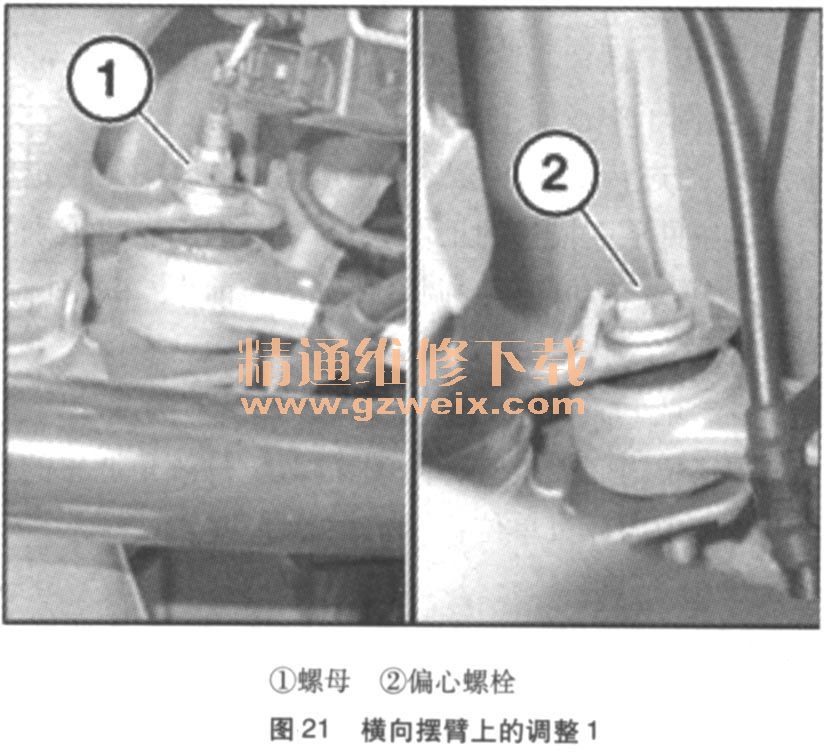
调整前更新螺母并以5Nm的力矩安装。转动偏心螺栓,直至达到中间设定值,拧紧螺母。摆臂上的调整:调整前更新螺母并以5Nm的力矩安装。
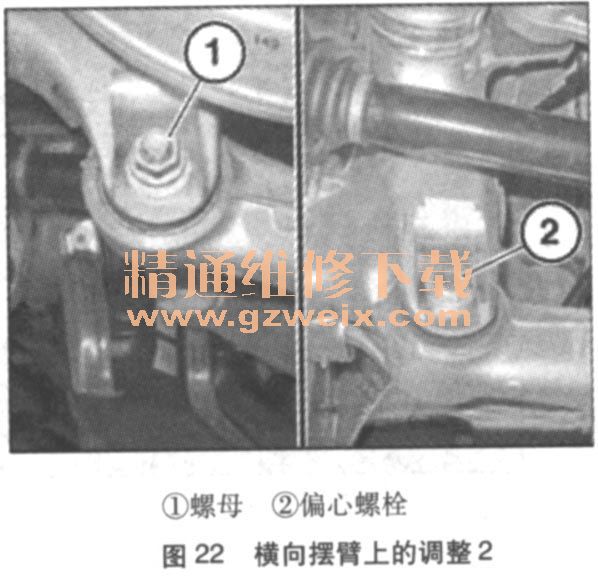
转动偏心螺栓,调整标准值,将螺母拧紧。依赖图23所示的前束/
车轮外倾角调整(用于打印和记录数值):
上一页 [1] [2] [3] [4] 下一页