3.1工艺方案的改进
通过对改进前工艺方案的分析发现鼓部与辐条交接处缩孔缩松严重,与实际生产中的铸造缺陷相吻合,因此需要进行工艺设计的改进,以下主要从两方面来做出改进:
a)产品(砂芯)设计方面:修改砂芯结构(如图6所示),增大铸件鼓部与辐条对应处的壁厚以增大和加宽补缩通道,进而增强补缩能力。温度场分布的目的,从而有利于加快孤立液相区的冷却速度,最后减小甚至消除此部位的孤立液相。
3.2改进后方案的铸件凝固过程分析
由于此次工艺方案主要是针对铸件凝固阶段的改进,而且通过对改进后的工艺方案的充型过程的模拟,发现其在改进前后的各项指标都变化不大,包括其充型时间,充型温度等,故在此不再展开赘叙,我们主要来验证铸件的凝固过程。
改进后的工艺方案的凝固过程数值模拟结果如图8所示。
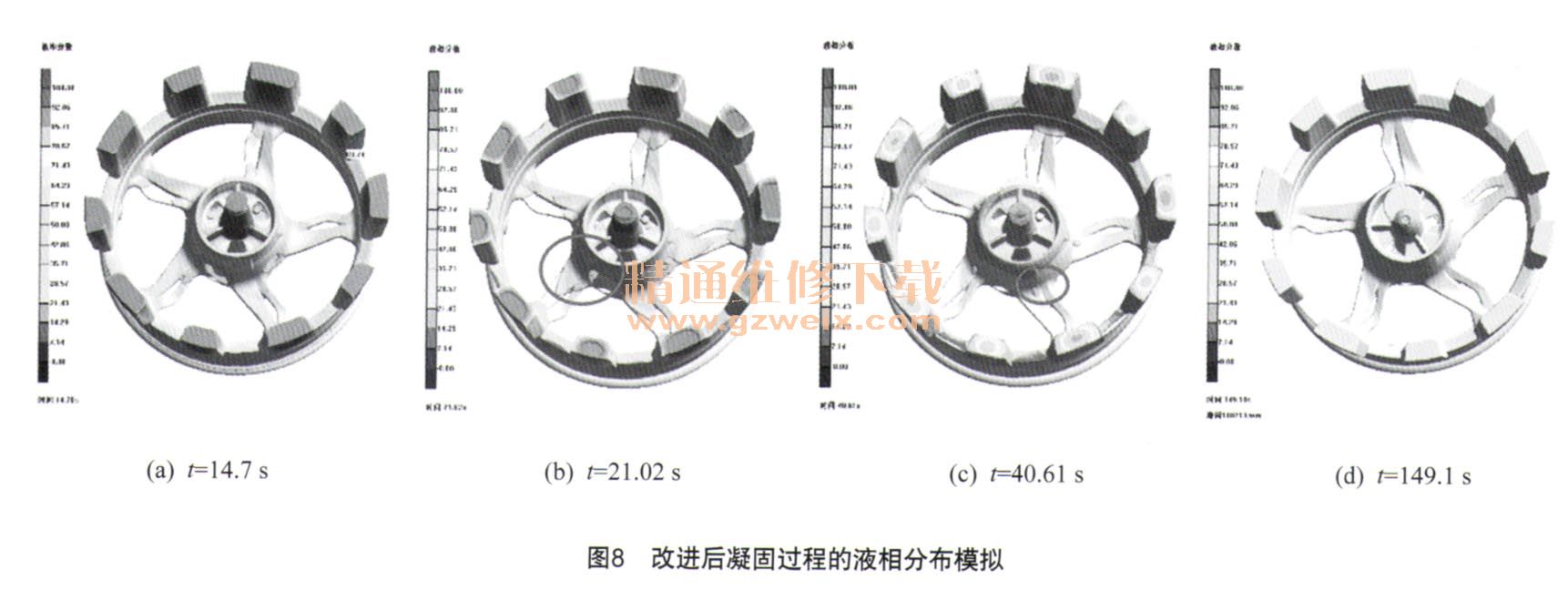
在第14.7 s(包括了充型时间),铸件的凝固液相跟改进前的方案差别不大。第21.02 s时,辐条与鼓部交接处跟中心浇口的补缩通道依旧很畅通,而在改进前的方案中此部位已经产生了严重的孤立液相区。第40.61 s时,辐条与鼓部交接处生成了微小的孤立液相区,微小的孤立液相区有望在后期的固态收缩[3]中消除。第149.1 s时,铸件已基本完全凝固,相比之前方案的180.61 s,大致缩短了31.5 s,这也为提高班产、增加企业技术经济效益起到了积极的作用。
3.3改进后方案的铸件缺陷(缩孔缩松)判定
对于改进后的方案,同样的我们也对其进行了缩孔缩松缺陷的检测,如图9所示
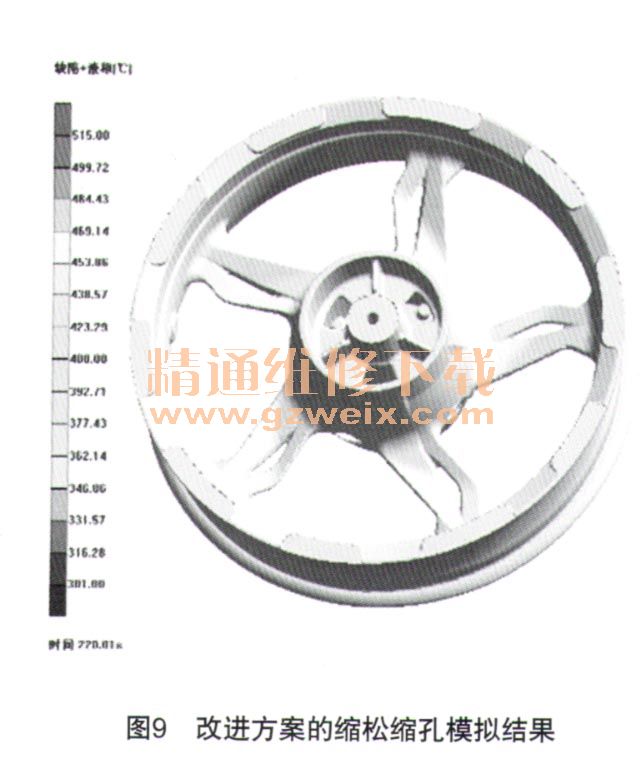
从图中可以看出,鼓部与辐条连接处并没有产生缩孔缩松缺陷,说明之前那些微小的孤立液相区依靠后期的固态收缩进行了自补缩,在最终凝固后的铸件中没有出现缩孔缺陷,从而保证了铸件质量。
在理论上确定已经解决了该铸造缺陷后进行了现场的小批量试制验证,通过品管部门检测后可知,原工艺方案中的缩孔缩松缺陷已经消失,也就是说改进后的工艺方案在实际生产中效果很好,成功地实现了本次改进的目的,并提高了铸件的下机合格率和班产,为公司取得了良好的技术经济效益。
4 小结
a)经小批量试生产,并随机抽取了10个样品进行X光检测,其疏松等级均符合客户的产品接收标准,表明模拟所得的优化工艺方案效果很好。
b)在该改进后的工艺方案下经过多次的重复浇注实验后,发现其所生产出的铸件基本未再出现严重的缩孔缩松缺陷,表明该工艺方案比较稳定,可以推广到量产使用。
c)通过两个工艺方案的对比,改进后的方案比改进前的方案出现孤立液相区的时间更靠后,体积更小,更分散,因此不管是从理论还是实际上来说,本次工艺方案的改进都是相当成功的。并且改进的工艺方案在铸件凝固所需时间方面也比改进前的方案快了31.5 s、因此生产部门可以适当加快生产节奏,提高班产,从而为本公司带来一定的技术经济效益。
上一页 [1] [2] [3]