2 整改措施
a)依据在供应商现场对下连板与立管压装前后尺寸的变化,为提高产品的可靠性,下发技术通知修订了产品标准,加大了下连板与立管的配合过盈量。结合供应商现场工艺设备加工精度,将前叉立管组件的下连板内孔按φ34、立管外径按φ 34控制。最大过盈量为0.14 mm,最小过盈量为0.03 mm。
b)立管外圆(与下连板配合部分)表面按

控制,下连板内圆表面按

控制。
c)为避免个别不合格下连板混入压装工序,前叉立管生产厂家在下连板内孔、立管外径加工工序增加了刀具调整后首检检查确认,首检确认合格之前的零部件全部隔离,合格后方批量生产。同时在生产过程中要求操作人员每2小时对加上尺寸检测一次,每次3-5件;并做好详细记录。
d)在下连板立管压装工序增加了压装力不足报警装置(见图6所示),从根本上杜绝了配合过盈量不足而压装将不合格产品流入下道工序的发生。从工艺上保证孔轴的配合过盈量。
3 后续追踪
产品整改2个月后又到生产厂家现场进行整改情况验证,现场抽查下连板、立管检测结果如表5所示。
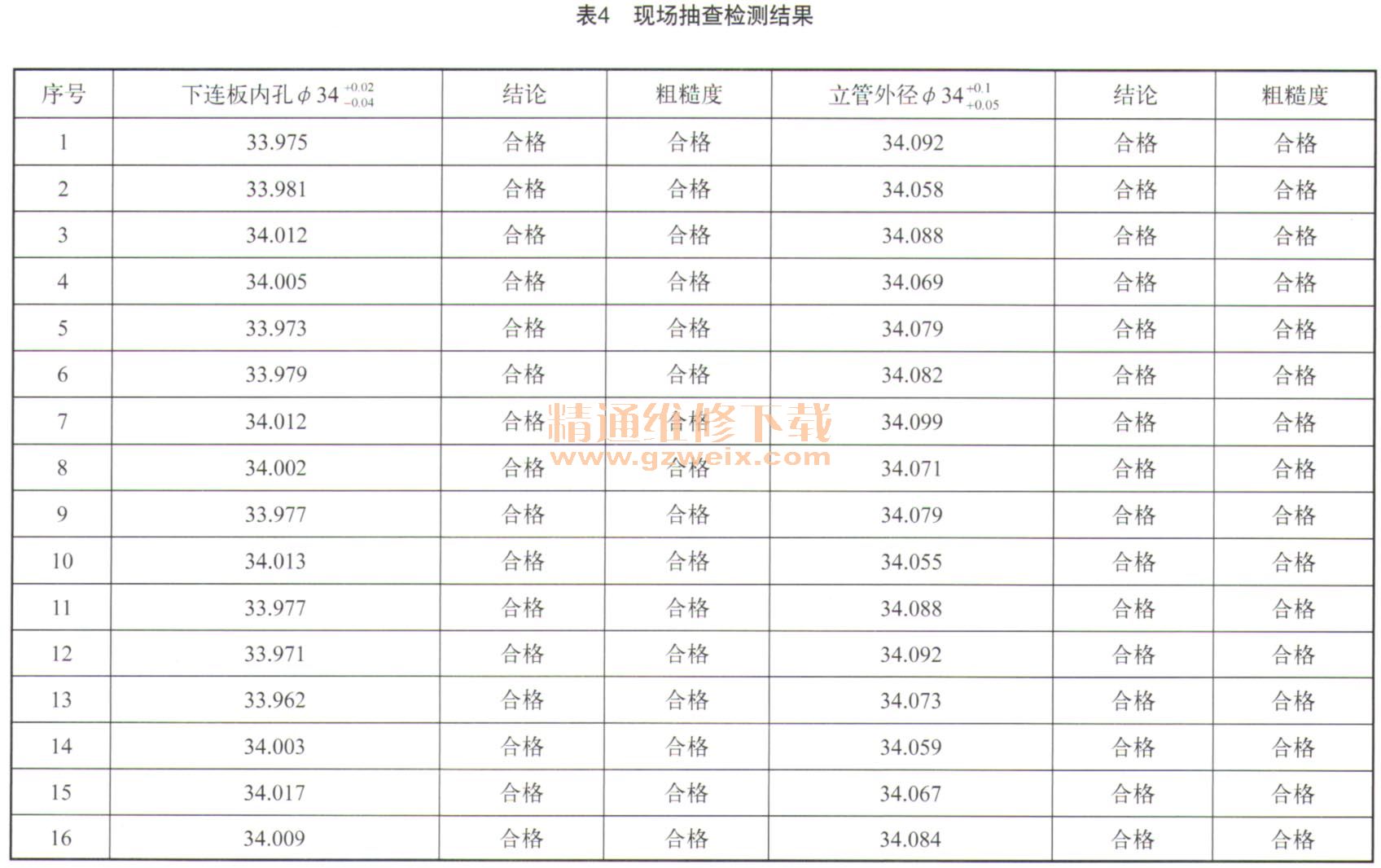

同时对压装报警设备观察压装50件,设备工作正常。说明生产厂家的工艺控制是完全有效。
改进后的前叉立管经过5万km各种复杂路况道路试验后,对整车进行拆解检测,未发现前叉立管开裂现象。说明整改措施是有效的。同时对公司现有的其他品种的前叉立管进行排查,消除质量隐患。
上一页 [1] [2] [3]