2 连接方式及质量隐患
2.1连接方式
图7是最普通的一种单支板连接方式,在支板上有螺纹孔,圆头螺栓穿过垫圈,下接头轴孔,旋入支板的螺纹孔中锁紧。
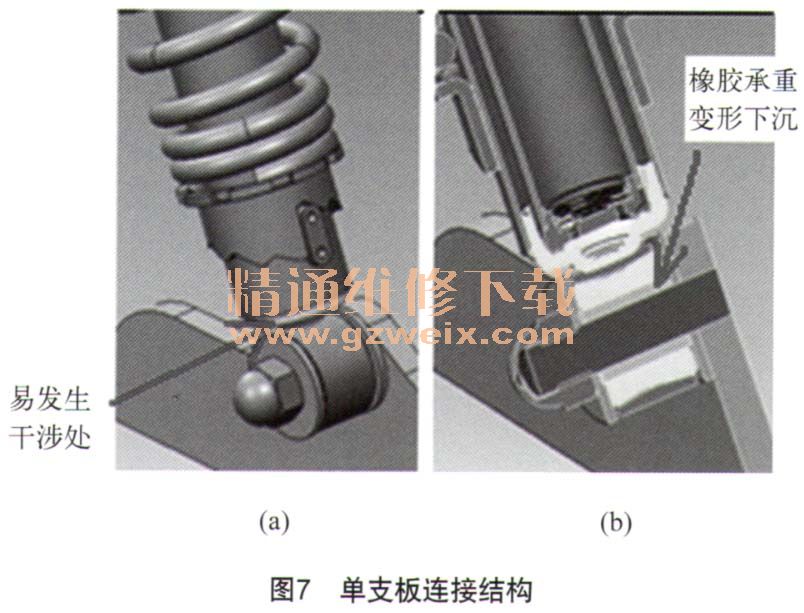
图A是一种双支板连接方式,双支板L有两个对同轴度有要求的孔,带肩螺栓穿过支板一侧,下接头轴孔,支板另一侧被带肩螺母锁紧。
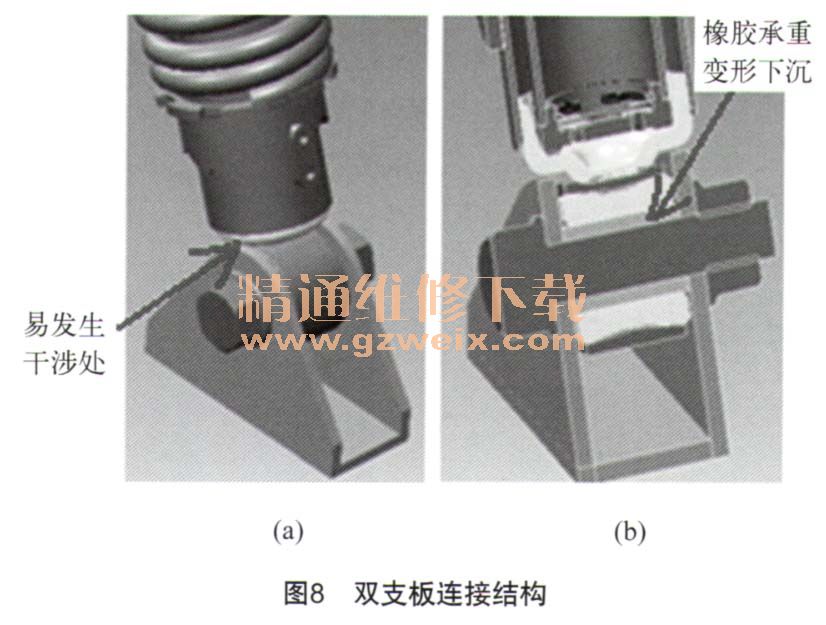
图9是一种块状支撑U型支架,在嵌有如同图2式样的内外钢件衬套中间有硫化橡胶的组合衬套,也达到了自定心的目的。
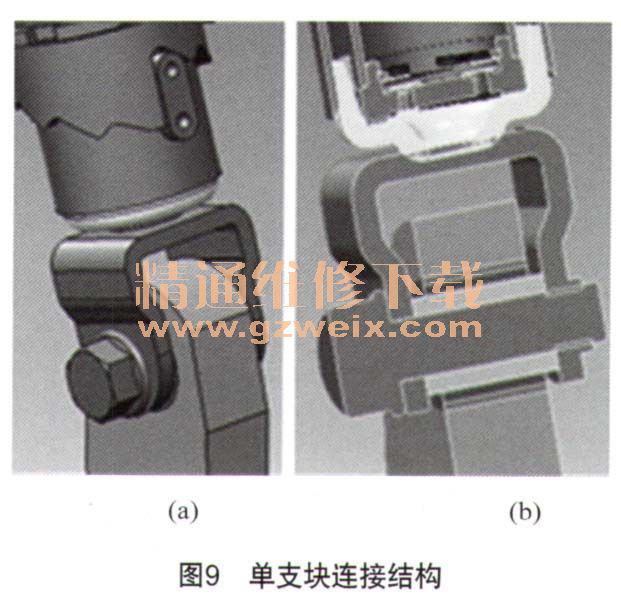
摩托车后减震器接头的式样有多种,支撑的样式可能略有变化,但是连接到车体上的无外乎上述的3种。
2.2质量隐患
后减震器断裂在市场时有发生,大多数是活塞杆螺纹根部断裂,因为这里是应力集中区域,当往复运动中心受阻卡滞,该部位最易形成疲劳断裂;也有与接头焊接部位撕裂,这种属于焊接厚度过簿,熔焊点小(<φ 6.0 mm),不在本文的讨论范围。下面是一些典型的故障实例。
后减震器上接头与车架连接,支撑车身;下接头与后轮、或者发动机后侧连接,承受来自地面的弹跳及车身的负荷。后减震器要往复运动,总会存在配合间隙。图10为一款设计比较苛刻的后减震器,极限偏移在0.156 mm,下接头内装有滚针轴承,轴衬与螺杆配合间隙0.4 mm。上接头结构如图2所示。
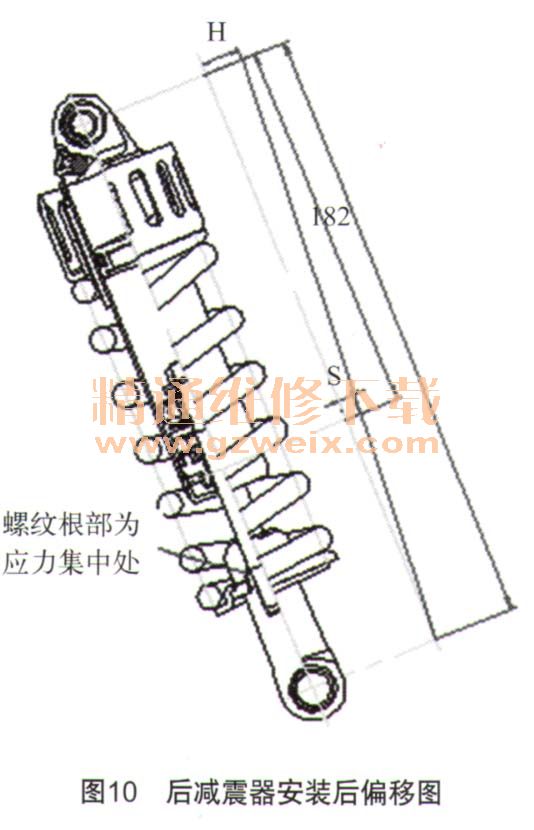
S=0.062 mm(最大配合间隙)
H--0.156 mm(最大偏移量)
正常情况下,上接头内的橡胶(NBR )隔层φ=3.5 mm,是完全可以修正0.156 mm的偏移量。但是如图11 (a)所示,连接是双支板支架,设计空间比较狭小,支架底部与接头圆弧顶部距离极限状态0.7mm;(b)所示行驶中堆积的泥沙排不出去,致使接头圆弧不能随着后减震器往复运动做适度转动;滚针缝隙被泥沙填满无法转动,逐渐卡滞使得活塞杆断裂;(C)滚针、衬管、螺母、垫片锈蚀也是接头不能适度转动的原因;(d)所示为活塞杆断面,箭头所指为运动受阻,活塞杆螺纹根部受剪切应力,逐渐被撕裂,最终断裂;(e)所示接头被泥沙卡滞,强制转动被干涉磨损的痕迹。
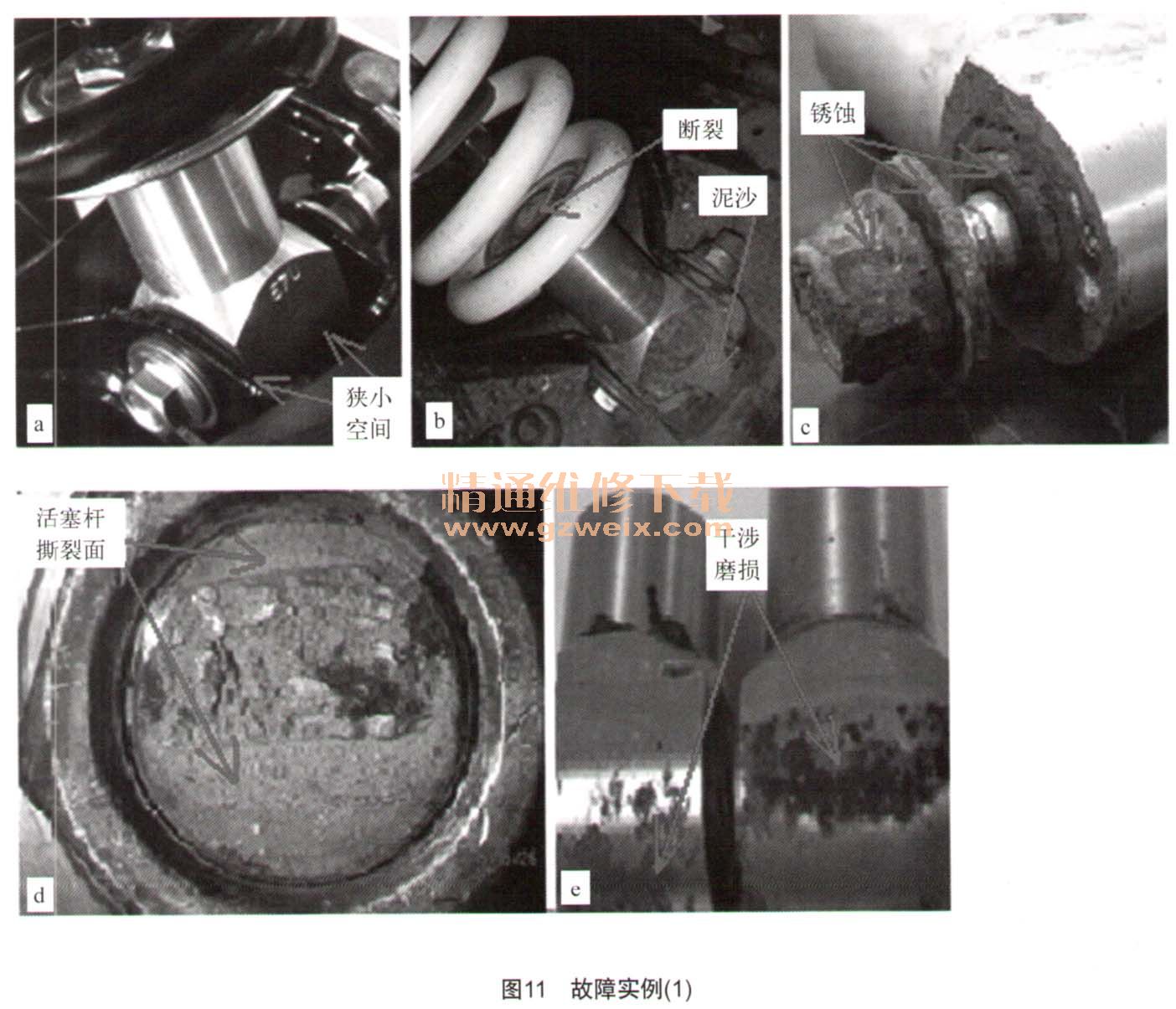
这种典型的设计误区在整车设计或者减震器设计上时有发生。图12 (a)所示,连接是双支板支架,设计空间比较狭小,调整座与支板几乎没有间隙;(b)、(c)橡胶隔层簿仅b =1.5 mm,橡胶绍尔硬度<75、橡胶粘接也不牢靠,承重后橡胶疲劳挤烂,致使后减震器丧失基本功能。
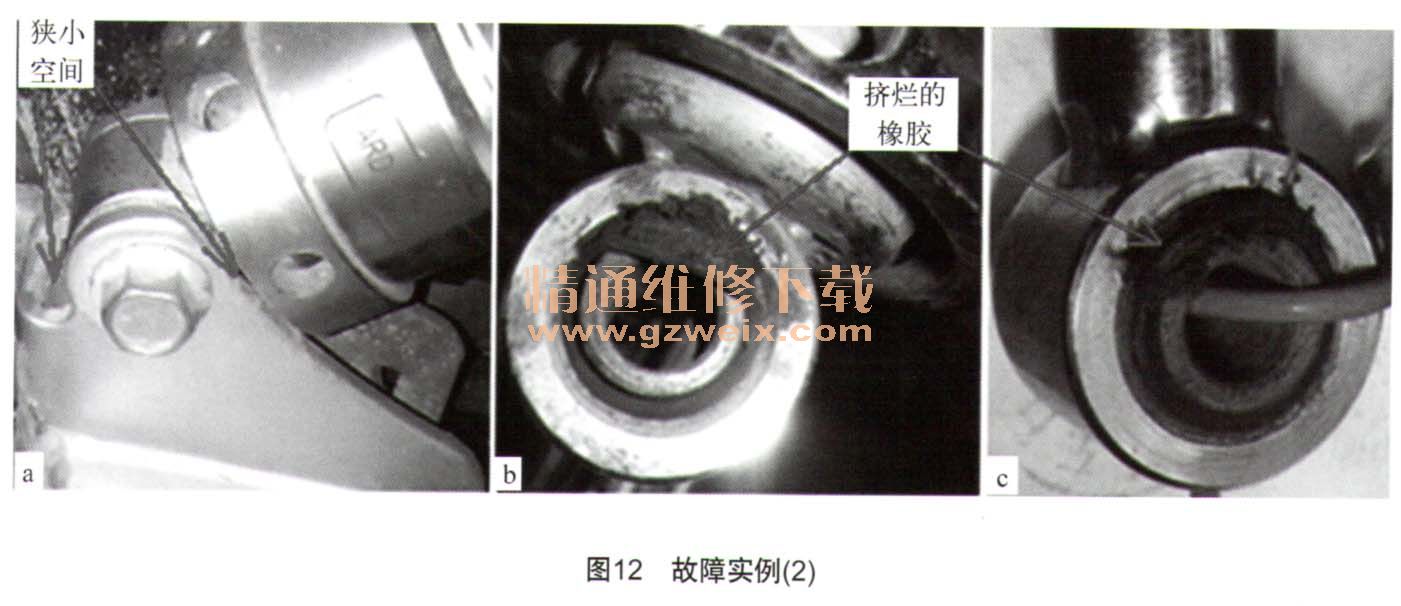
图13 (a)所示,设计空间是足够大,但是在安装中时常出现偏装卡滞如图(c),结果致使后减震器运动不畅,活塞杆根部受侧向应力断裂。
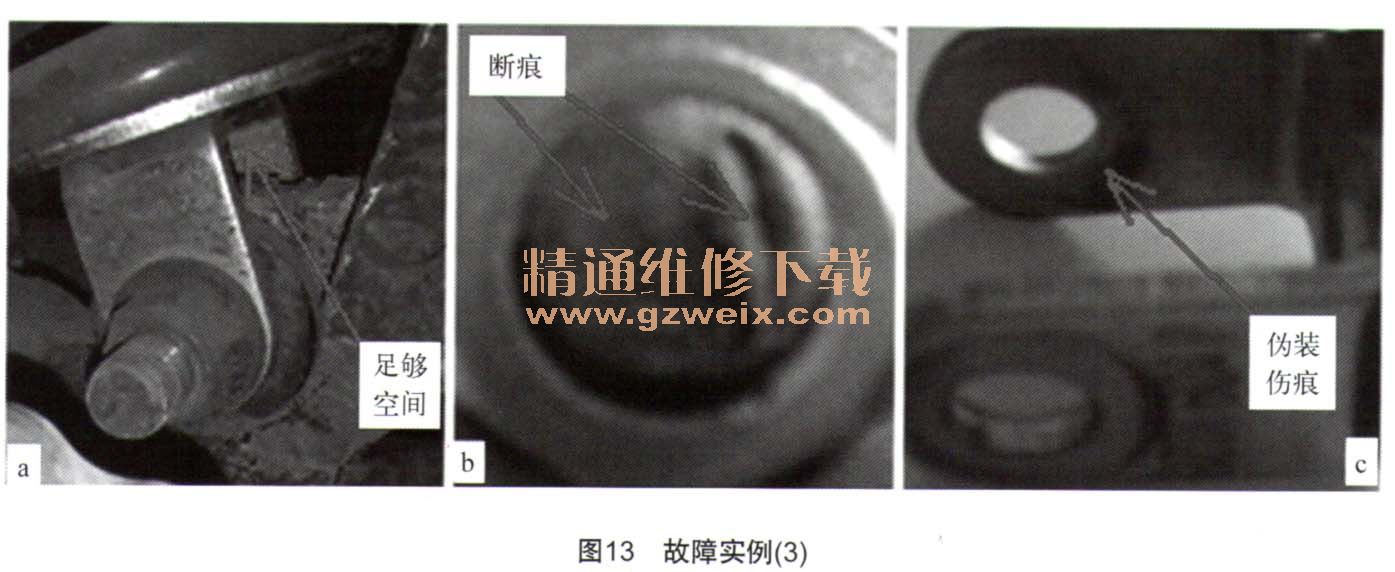
大部分故障为干涉断裂,主要在如图7 (a),图8 (a)在设计上过于紧凑,对橡胶隔层变形没有预留足够空间。但如图11所示的情况也属罕见。
上一页 [1] [2] [3] [4] 下一页