⑧使用完毕,应将旋具擦拭干净。
3.锤子
(1)分类锤子的种类有钢制圆头锤、横头锤、软面锤等,如图1-20所示。
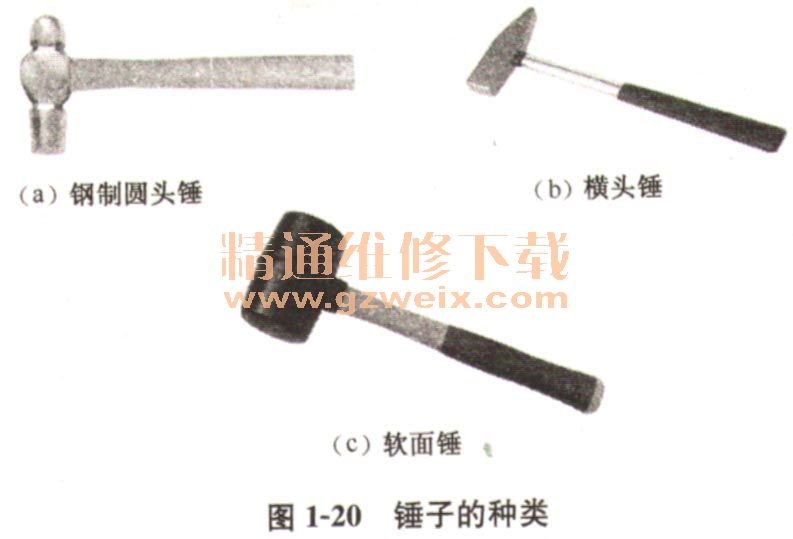
(2)用途、用法与规格
①钢制圆头锤。钢制圆头锤是在拆装较硬组合时使用。钢制圆头锤和横头锤的规格是以锤头的质量单位规定的。常用的有0. 25kg、0. 5kg、0. 75kg、1kg、1. 25kg和1. 5kg六种。
②横头锤。横头锤是在维修饭金等用力不大的零件时使用。横头锤的规格与钢制锤基本相同。
③软面锤。软面锤一般用于过盈配合的组合件的拆装,当敲开或压紧组合件时,使用软面锤不会使零件产生损坏。常用的有塑料、皮革、木质和黄铜软面锤。
(3)使用注意事项
①使用前,必须检查锤柄是否安装牢固,如松动应重新安装,以防在使用时由于锤头脱出而发生伤人或损物事故。
②使用时,应将手上和锤柄上的汗水和油污擦干净,以免锤子从手中滑脱而发生伤人或损物事故。
③如图1-21所示,在使用锤子时,手要握住锤柄后端,握柄时手的握持力要松紧适度,这样才能保证锤击时灵活自如。
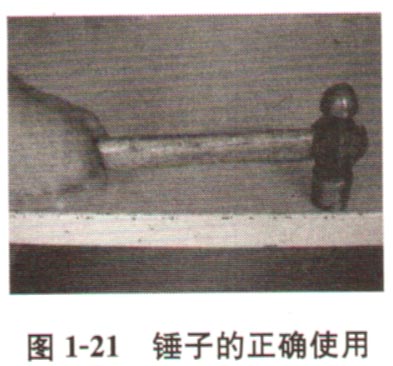
锤击时要靠手腕的运动,眼应注视工件,锤头工作面和工件锤击面应平行,才能使锤面平整地打在工件上,不能有如图1-22中所示的操作方法。
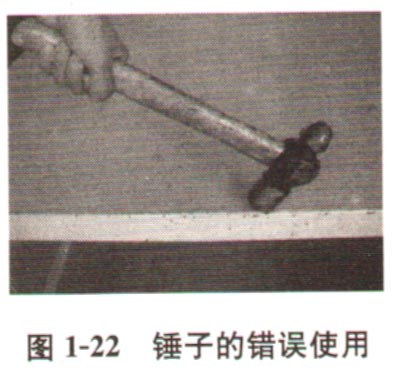
④使用前,应清洁锤头工作面上的油污,以免锤击时发生滑脱而敲偏,损坏工件或发生意外。
⑤在锤击铸铁等脆性工件和截面较薄的零件或悬空未垫实的工件时,不能用力太猛,以免损坏工件。
⑥使用完毕,应将锤子擦拭干净。
4.扳手
(1)分类扳手的种类有呆扳手(双头)、梅花扳手、套筒扳手、活扳手、管子扳手、扭力扳手和专用扳手等,其中套筒扳手又由套筒头、套筒头手柄、长接杆、棘轮扳手等组成,如图1-23所示。
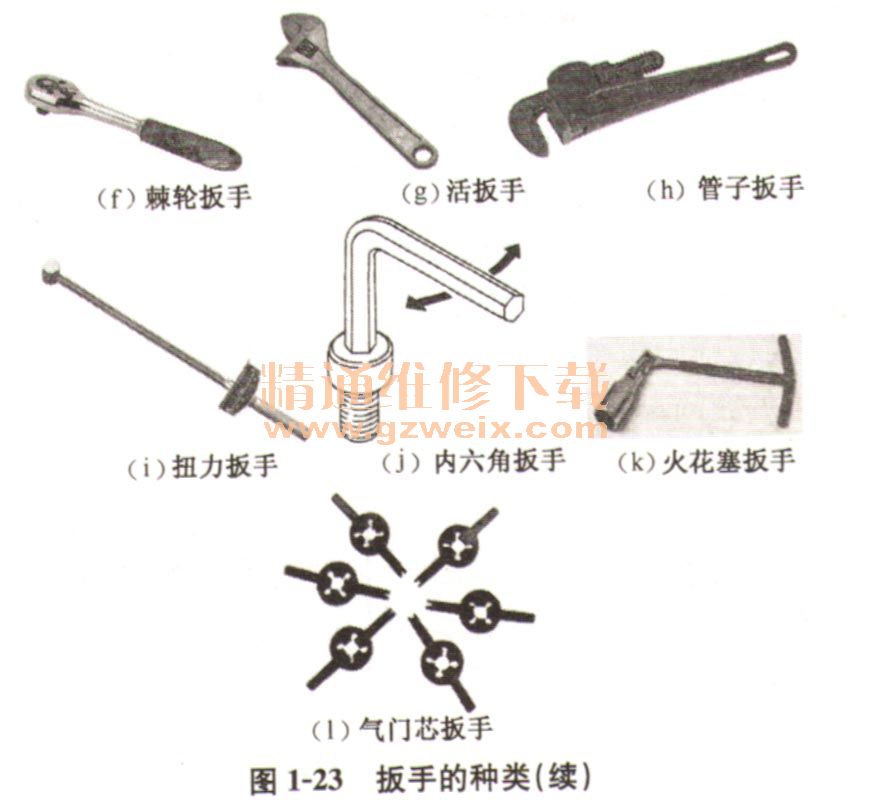
(2)用途、用法与规格
①呆扳手(双头)。这种扳手主要用于拆装一般标准规格的螺栓或螺母。使用时可以上、下套入或直接插入,具有使用方便的特点。常用的有6件套、8件套两种,适用范围在6~24mm之间。按其结构形式可分为双头扳手和单头两种;按其开口角度又可分为15°、45°、90°三种。
②梅花扳手。梅花扳手两端是套筒式圆部分或全部围住,从而保证工作的安全可靠性。其用途与呆扳手相似,具有更安全可靠的特点。常用的有6件套、8件套两种,适用范围在5. 5~27mm之间。
③套筒扳手。套筒扳手适合拆装部位狭小、特别隐蔽的螺栓或螺母。其套筒部分与梅花扳手的端头相似,并制成单件,根据需要,选用不同规格的套筒和各种手柄进行组合。如活动手柄可以调整所需力臂;棘轮扳手用于快速拆装螺栓、螺母。有的扳手同时还能配用扭力扳手显示扭紧力矩,具有功能多、使用方便、安全可靠的特点。套筒扳手是一种组合型工具,使用时由几件共同组合成一扳手。常用的套筒扳手有13件套、17件套和24件套等多种规格。
④活扳手。主要用于拆装不规则的带有棱角的螺栓或螺母。活扳手的开口端根据需要可以在一定范围内进行调节。
⑤管子扳手。是一种专门用于扭转管子、圆棒以及用其他扳手难以夹持,扭转光滑的圆柱形工件的工具。管子扳手的开口端根据需要可以在一定范围内进行调节。
⑥扭力扳手。在维修作业中,凡是有扭紧力矩要求的螺栓或螺母,均需用扭力扳手将螺栓或螺母拧到规定力矩。是一种与套筒扳手中的套筒配合使用,能显示扭转力矩的专用工具。用扭力扳手拧紧螺栓或螺母时,其转矩的大小能及时指示出来,扭矩的单位是N·m。汽车维护中常用扭力扳手的规格为0~300N·m。
⑦内六角扳手。用于扭转内六角头部的螺栓。一般是不同规格的成套工具。
⑧火花塞扳手用于拆装火花塞。
⑨气门芯扳手用于拆装轮胎气门芯。
(3)使用注意事项
①呆扳手(双头)。
a.一定要选择与所拆装螺栓(螺母)相同规格的扳手,如图1-24所示。
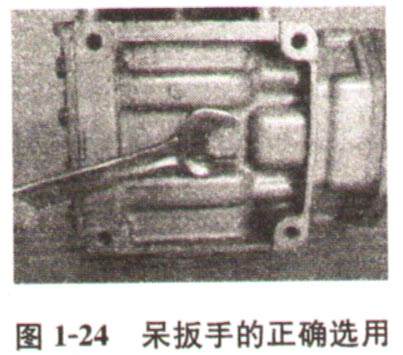
b.如图1-25所示,不要使用尺寸过大的扳手,以免因扳手尺寸过大而损坏螺栓(螺母)的棱角。
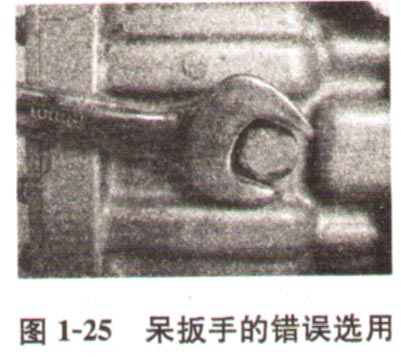
c.当使用推力拆装时,应用手掌力来推动,如图1-26所示
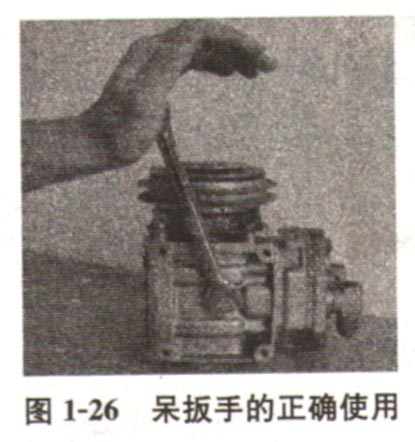
d.如图1-27所示,不能采用握推的方式,以免碰伤手指。
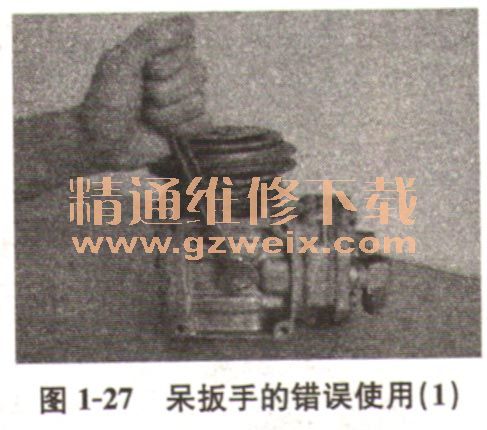
e.如图1-28所示,不能采用两个扳手对接或用套筒等套接的方式来加长扳手,以免损坏扳手或发生事故。
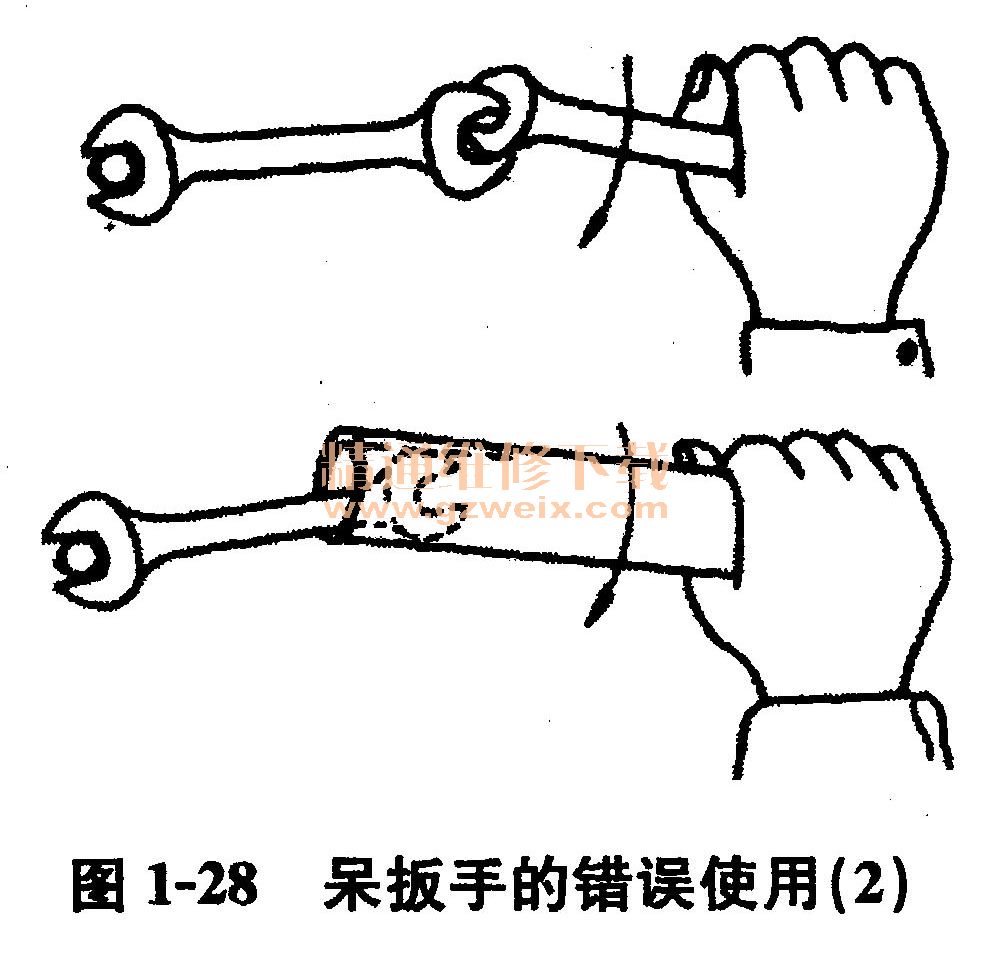
②梅花扳手。使用注意事项与呆扳手相同。
③套筒扳手。使用时一定要选择与所拆装螺栓(螺母)相同规格的扳手。
④活扳手。使用时必须将活动钳口的开口尺寸调整合适,用力要均匀,以免损坏扳手或使螺栓、螺母的棱角变形,造成打滑而发生事故。应使扳手的活动钳口承受推力,固定钳口承受拉力,正确的使用如图1-29所示。

错误的使用如图1-30所示。
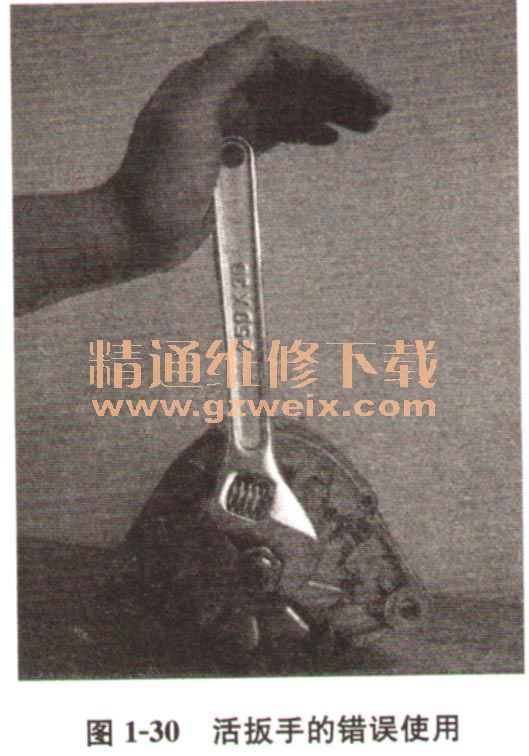
⑤管子扳手。由于管子扳手的钳口上有齿槽,使用时应尽量避免将工件表面咬毛;另外不能用管子扳手代替其他扳手来旋转螺栓、螺母或其他带有棱角的工件等,以免损坏螺栓、螺母等棱角。
⑥扭力扳手。使用扭力扳手,必须符合规定,切忌在过载情况下使用而造成扭力扳手的失准或损坏。用完应将扭力扳手平稳放置,避免因重物撞、压,造成扳手杆或扳手指针变形而影响扳手的精度,甚至损坏扳手。
5.顶拔器
(1)分类顶拔器的种类有两爪顶拔器、三爪顶拔器、球轴承顶拔器、圆锥滚子轴承顶拔器等,如图1-31所示。
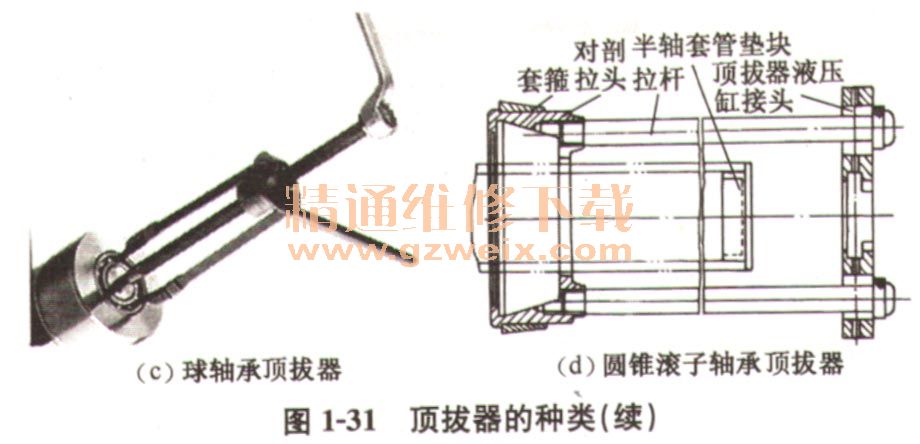
(2)用途与用法
①两爪顶拔器。主要用于拆卸发动机曲轴正时齿轮、曲轴带轮、风扇带轮、凸轮轴正时齿轮及其他位置尺寸合适的齿轮、轴承凸缘等圆盘形零件。
②三爪顶拔器。三爪顶拔器主要用于拆卸各种齿轮及其他轴承、凸缘等圆盘形构件。
③球轴承顶拔器。专用球轴承顶拔器一般按某一轴承尺寸制作的,主要用于该种类型号的球轴承的拆卸。拆卸轴承时,将两爪扣进球轴承钢球之间的空档,装上锁紧套,拧转顶拔器的螺杆,就可以将轴承拉下来。
多用球轴承顶拔器,使用时先将拉脚插入球轴承内、外座圈之间,再插入插脚夹紧。然后顺时针转动手柄,使螺杆下移,则顶头顶住轴当轴承距轴端近时可去掉接杆,只用拉脚即可。使用中换用不同规格的拉脚,可拉下多种球轴承和曲轴正时齿轮。
④圆锥滚子轴承顶拔器。主要用于主减速器主动锥齿轮轴承的拆卸。使用时,先利用螺杆将垫盘提起,将拉爪从轴承侧面装入,然后转动螺杆使垫盘卡入工作中心孔,与拉爪的卡拔部位对中并限位,以防卡偏和受力时脱滑。继续转动螺杆即可将轴承内套拉下,如图1-32所示。
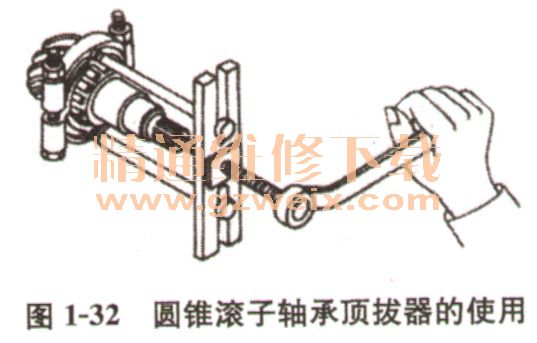
这种顶拔器只能用在轴承内套里面高出轴肩较多、端面间隙较宽松的场合。
(3)使用注意事项
①使用两爪顶拔器和三爪顶拔器时,当顶拔器与被拆工件安装好后,要检查拉爪是否卡紧,两边受力是否均匀对称,垫套与轴是否对中,然后扭动螺杆接触工件后,再复查一次,确认无误后,才能进行拆卸工作。
②使用球轴承顶拔器和圆锥滚子轴承顶拔器时的方法与两爪顶拔器基本相同。
6.铲刀
铲刀的实物如图1-33所示。铲刀的用途是铲除零件上的积炭、油泥等杂物。
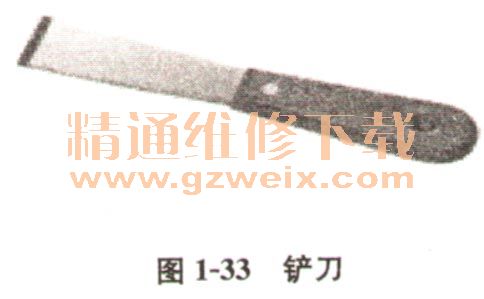
7.钢丝刷
钢丝刷的实物如图1-34所示。钢丝刷可清除零件表面的油污等杂物。钢丝刷的硬度较大,如果用于清洗相关零件时,容易给表面造成磨损或者划伤。因此,使用时用力不可过大。
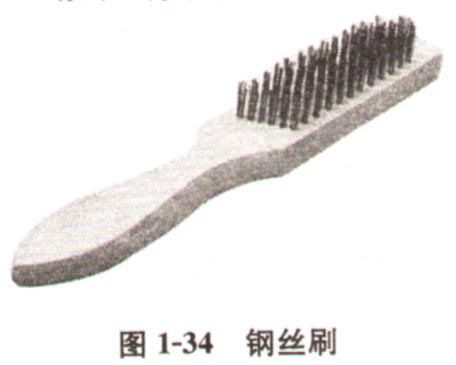
8.镊子
镊子的实物如图1-35所示。用镊子可夹取细小的零件等。使用时,用大拇指和食指夹住镊子,使镊子后柄位于掌心,而加上中指。使用镊子时,注意不要太用力,以避免手发抖
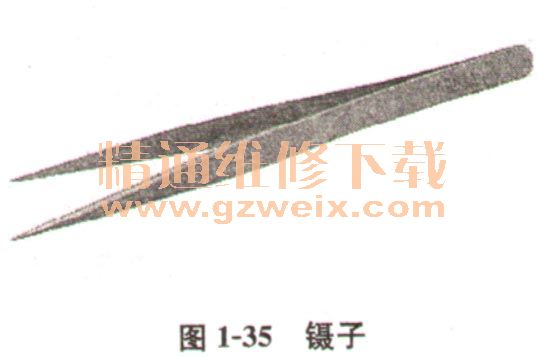
9.冲子
冲子的实物如图1-36所示。冲子可以用于冲出直的或有销钉。冲子通常以几种尺寸配成套,每套3~5只。使用注意事项:
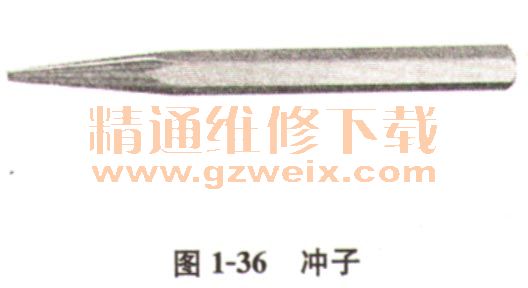
①销钉移动或部分地从孔中冲出后,冲子就不要再鉴用了。
②所选用的圆凿和与孔眼相匹配的尖冲头的尺寸要尽可能大,使用时注意,绝不能使用尖冲头开始冲销钉。因为其冲柄较细,不能承受大的冲击负荷。否则,冲柄就会弯曲或折断。
③因为有的冲头较尖,在硬金属上一般不得使用冲子。
10.数子
錾子的实物如图1-37所示。
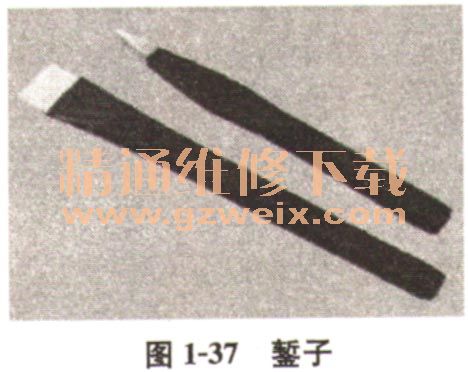
(1)用途、用法与规格 錾子是一种靠锤子敲击来对金属工件进行切削加工,可以除去毛坯的飞边、毛刺、浇冒口,切割板料、条料,开槽以及对金属表面进行粗加工等。规格一般为160×13mm、150×3mm(长×数口宽)。
(2)使用注意事项
①使用时防止锤头飞出。
②使用时应及时磨掉茎子头部的毛刺。
③操作者应戴上防护眼镜,工作地周围应装有安全网。
④经常对錾子进行刃磨,保持正确的后角,契削时防止錾子滑出工件表面。
11.油石
油石的实物如图1-38所示。油石是供手工研磨使用的一种磨具。广泛用于手工修磨各种工具、模具和零件。油石比较容易断,使用时应注意。
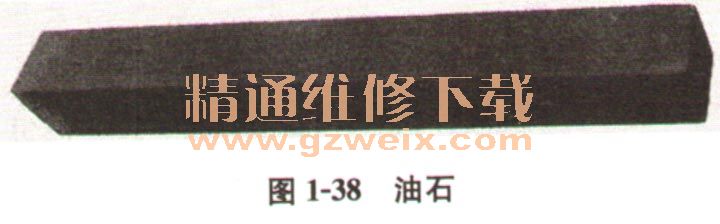
上一页 [1] [2] [3] [4] [5] [6] [7] [8] [9] [10] [11] [12] [13] [14] [15] [16] [17] [18] [19] [20] [21] [22] [23] [24] [25] [26] [27] [28] [29] [30] [31] [32] [33] [34] 下一页